A new indoor hydroponic technology that raises live, green fodder from seed to feed in six days is starting to disrupt the way livestock is fed on farms around the world.
Bill Vanderkooi has been testing the Hydrogreen system on his Abbotsford, B.C. farm for the past two years with his 250 head of grass-finished beef cattle.
Three months before slaughter, Vanderkooi feeds his Angus-Holstein cross steers a finishing ration of grass silage and Hydrogreen wheat grass with minerals, plus free-choice liquid whey.
“We’ve had great results in terms of performance and quality — they’re mostly grading AAA, which is unusual for grass-finished animals,” he says.
Read Also
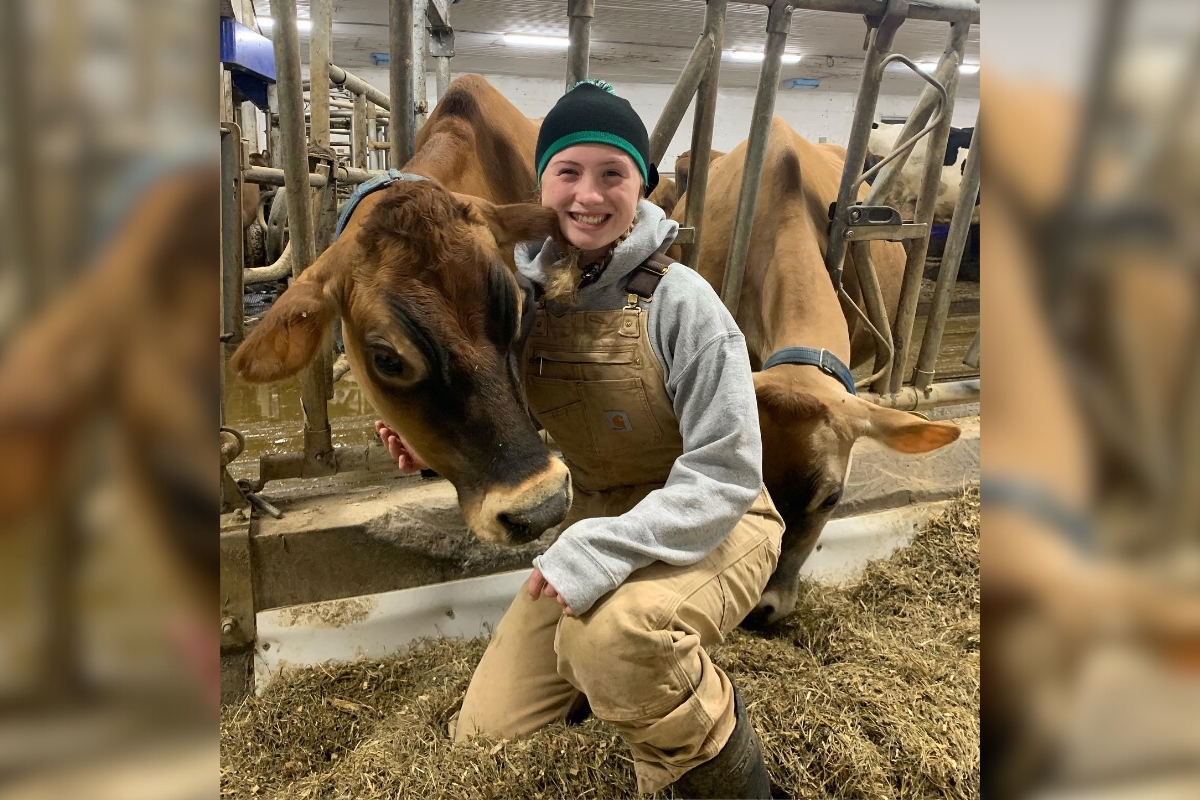
Youth focused on keeping Quebec’s dairy industry strong
In part two of our Making the Future series, Country Guide spoke with Béatrice Neveu from Rawdon, Que. (Read part…
The Hydrogreen growing system is fully automated. One operator using a control panel at the end of the machine can do all the seeding, watering, lighting, fertilizing and harvesting work by pushing buttons. Vertically stacked growing surfaces are mechanically seeded, usually with wheat or barley. One pound of seed will produce five pounds of feed in six days.
At Vanderkooi’s Bakerview EcoDairy, Hydrogreen machinery produces a continuous, year-round supply of green fodder for his beef and dairy herds.
On the dairy side, he’s testing the equipment on his 45-cow herd as a substitute dry matter for grain in one total mixed ration (TMR), forage in another, and a control diet. The trial started in the fall of 2019 and will run until 2024. Data is being collected on milk components and volume, ruminant activity and cow health.
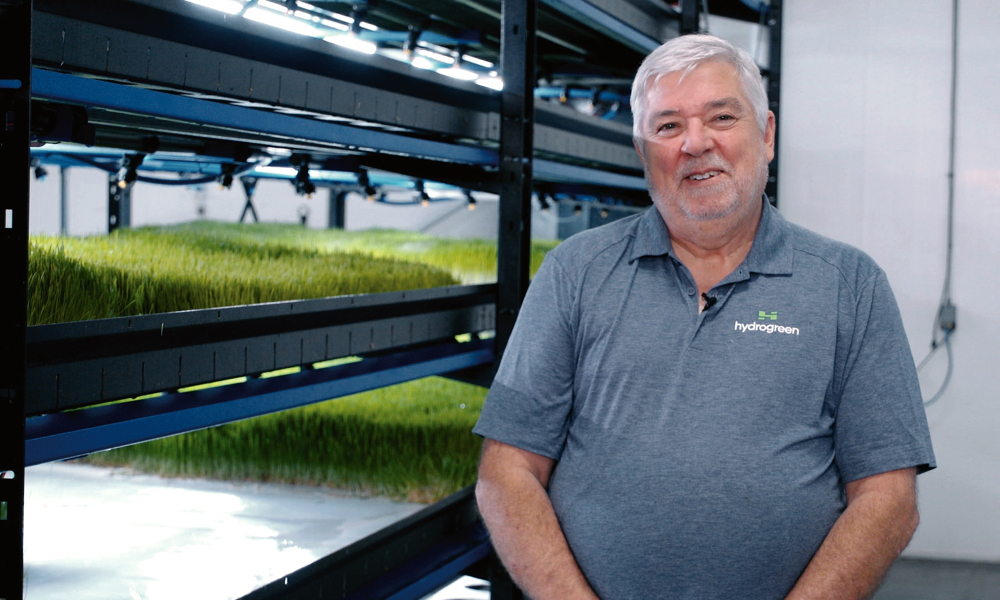
Hydrogreen’s beginnings
A few years ago, South Dakota-based rancher and inventor Dihl Grohs was looking for a way to more efficiently feed his Idaho beef herd. The state was experiencing some drought, and while he was intrigued by some experimental dairy feed systems that used sprouted barley in pans, there was still too much labour involved. So he hit on the idea of an automated conveyor belt.
While the cattle loved the product, the automation piece wasn’t falling into place. That’s when he met and tapped Craig Livingston, a fellow South Dakotan who has a background in computers, sales and marketing —and startups.
“We drew up some business plans, crunched some numbers and decided that it looked really feasible,” Livingston says.
Six years later, Livingston is the vice-president of Hydrogreen, a company that has merged with Cubic Farm Systems Corporation, which grows hydroponic food for people in British Columbia.
“It took us about three years of R&D to get a piece of equipment that would really do the job,” he says. “It takes a lot of time and money — especially when you’re doing something no one has ever done before.”
Livingston says farming is a traditional industry and the technology was a significant change to how animals were fed. The toughest challenge was finding a handful of early adopters who understood the company’s vision, listened to the science backing their technology and were willing to take the time to understand the economic and nutritional benefits.
This also helped with marketing the technology — by leveraging the results of the early adopters and “showing and telling” others.
After several changes of direction, many sleepless nights and visits to robotic dairies, they decided on a fully automated system.
“We needed to get to a place where you could do everything with the push of a button,” Livingston says, adding that the company received a great deal of help from an Iowa patent attorney who also had a background in agriculture.
How it works
“We have a philosophy that change is good,” Livingston says. “We try to make the product better every day.”
Currently Hydrogreen is being marketed to the dairy, beef and equine sectors, but they’re looking to expand into goats, poultry and other livestock in the future.
The equipment is fully customizable to what farmers need. Machine components are manufactured at the Sioux Falls, South Dakota factory and the main structure of the system is often fabricated nearer to the farm where it’s being installed.
“When we first started the business, we wanted it to be worldwide,” says Livingston. “So the system is basically an erector set.”
The steel for the frame can be cut by laser cutters which are available around the globe. Designs can be sent from Hydrogreen to wherever the client is situated.
The company then has crews that are sent to put the equipment together and train the farmer/operator on how to make it work.
Benefits
There were several upsides to building the business. They discovered, for example, that being able to control the growing environment produced better grass. While the original idea was to save labour, a number of other benefits became apparent.
In the lower mainland of British Columbia, for example, land prices are around $100,000 an acre, according to Vanderkooi. So, besides being interested in testing out the innovative equipment, he wanted to see if it paid off in terms of reducing land costs.
He has two buildings that house the machines. The smaller, 800-square-foot building holds two four-layer machines and the larger, 1,200-square-foot building holds two six-layer machines. Together, the Hydrogreen machines produce the equivalent of 50 acres of dry matter.
Last year, the total cost to Vanderkooi of retrofitting the 1,200-square-foot silage bunker plus the machines was $667,000.
Vanderkooi’s cautionary note about these savings is the need to adhere to manure management regulations and having enough land to accommodate the output. In other words, people have to be careful about what’s coming out of the animals as well as what’s going into them.
Still, with this system, greenfeed is available every day of the year and takes a fraction of the time, energy and cost to grow and harvest. The technology’s indoor location also means that there’s no risk of drought, disease or pests.
It also saves the costs and environmental effects of shipping grain into the province from Alberta and Saskatchewan.
Environmental effects
The advice from the company to anyone looking to bring a disrupting invention to market is to focus on helping farmers get closer to a net zero carbon footprint and to become more environmentally and socially sustainable.
A study recently submitted for publication by a team from the Food and Agriculture Institute of the University of the Fraser Valley concluded that “hydroponic farming of fodder could contribute to climate mitigation objectives if complemented with effective energy and land use policies.”
The research was conducted, in part, with the Bakerview EcoDairy’s Hydrogreen system.
The paper’s theory is that, with the pressures on animal agriculture to reduce greenhouse gas (GHG) emissions, but also with demand for meat protein continuing to climb, technological feed solutions are needed to lessen the effects of conventional agriculture’s carbon footprint.
Using equipment like Hydrogreen reduces the use of the land, nutrients and fossil fuels associated with conventional feed production by moving everything inside. The effects include “higher yields with much smaller footprints and lower water and nutrient consumption.”
Overall, the paper says the system produced 5.5 per cent fewer GHG emissions than conventional barley grain fodder and 23.2 per cent fewer emissions than alfalfa hay.
For the future
Livingston says that the merger with Cubic Farms has been very good for business. They’re expanding globally and have made sales in Sweden, Germany, Italy and a number of other countries. The company is connecting with distributors in the U.S. and around the world, and they’ve been looking for distributors in Ontario.
They’re continuing to refine the system and are conducting more research into how the feed affects such areas as animal nutrition and health. They sold 24 machines to a certified organic dairy farmer in Western Canada that are expected to be installed in early 2021 and have several more orders from across the country in the pipeline.
The COVID-19 pandemic hasn’t slowed the company down. In fact, Livingston says the staff in Sioux Falls has doubled over the spring and summer of 2020.
“We have talented people pulling in the same direction — it’s really fun to be part of it,” he says.
Livingston cites the fact that, in certain parts of the world, wars are waged over food, and if they can do something to help change that, it’s great.
“I can’t think of a downside to what we do,” he says. “We can make the animals healthier and happier, increase production and help farmers and ranchers — they’re all good things.”
Haiwick Heritage Ranch
Nick Ferens and Paula Haiwick’s South Dakota ranch was started by her grandparents in 1939, and the couple took up the reins in 2013, when Paula’s dad was slowing down.
They raise 300 head of Angus cows and directly sell the premium, dry-aged beef. They also have horses and sheep.
“We had a really tough drought in 2017,” Nick says. “So I started looking around for a better way to feed the cattle.”
After researching the market, he had a six-rack Hydrogreen system installed in 2018 in a purpose-built structure that can accommodate three more six-rack systems as the operation expands in the future.
He uses the Hydrogreen fodder primarily for his replacement heifers. For two years, he has fed a control group of five or six heifers rations that don’t include Hydrogreen.
“The heifers on Hydrogreen have averaged about 100 pounds of gain over the cows on the traditional diet over the same period of time,” Ferens says.
It takes him only an hour or so to feed the cattle for the day. He mixes in about 700 to 750 pounds of dry hay with the Hydrogreen fodder.
“I can put three (large square) bales out for 60 head and it’ll last for three days,” he says, adding that the hay consumption has decreased dramatically since he started using the automated system.
He’s had his rations tested and the amount of minerals he needs to add is “insanely small.” In fact, his nutritionist has at times recommended not adding any mineral supplements at all.
The consistency of the Hydrogreen fodder is also a benefit. Last year, for example, the protein content of his hay was very low — about 60 to 70 per cent of what he needed.
Rather than having to buy added protein content (alfalfa), he used more of the Hydrogreen fodder for his other cattle.
“Whatever the seed you use — wheat or barley — you have to make sure there’s good protein content,” he says.
His Hydrogreen equipment can produce the equivalent of 320 acres of South Dakota prairie.
Land is selling for $2,000 an acre and Ferens calculates that, if each cow/calf needs 10 acres, he could add 32 head of cattle on land valued at $640,000. Which makes his one Hydrogreen system that feeds 150 head of cattle a bargain at about $125,000.
While he had to build the structure and install a grain bin and vertical mixer, he figures he’s still ahead, with a break-even timeline of about eight years. This he compares with buying the land to allow him to run a single additional head — which would be closer to 45 years.
He also points out that the system isn’t subject to drought, frigid temperatures or massive snowfalls, and he says he’s very pleased with the customer service he has experienced, and appreciates that Hydrogreen staff have been quick to help him with the rare times he’s needed to reset the system or fix a wire.
He also finds the Hydrogreen fodder highly palatable for the cattle.
“They’re so happy when the feed comes out — they can’t get to it fast enough,” he says, adding that a side benefit is that he hasn’t had to clean out his feed bunks in two years because the cows do it for him.