For the past 10 years, Ben Hartman and his wife Rachel Hershberger have been running a Lean farm near Goshen, Indiana. That’s “Lean” meaning efficient and highly productive, not in the sense of barely surviving.
Today Hartman, author of The Lean Farm, is recognized as one of the United States’ leading experts on applying lean systems thinking to farms.
Although it was originally an industrial system, the principles of Lean adapt very well to the farm. Who wouldn’t want to eliminate waste, improve efficiency and workflow, and create more profit? That’s what Lean is designed to do, and there are a number of different Lean methodologies that have evolved over the years to do just that.
Read Also
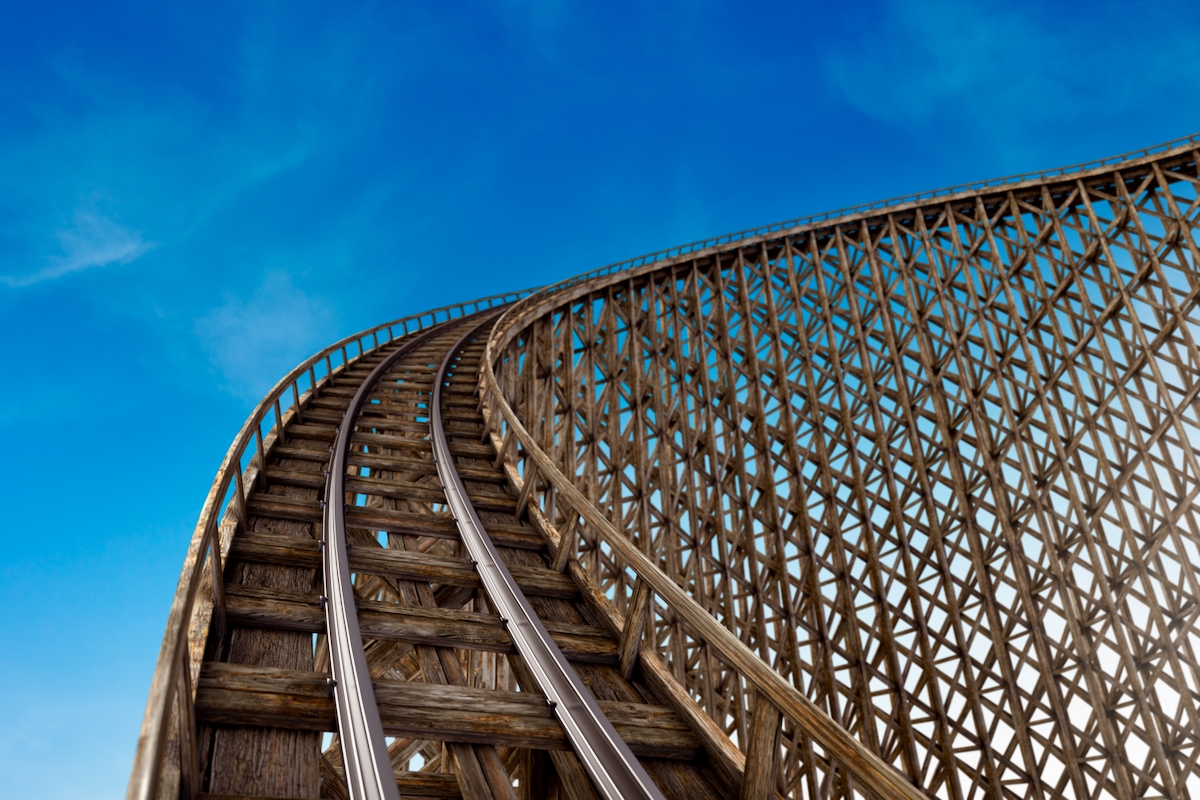
Riding the tariff rollercoaster
Farmers are accustomed to roller-coaster years. But the current geopolitical windstorm is something else entirely. On his cattle operation near…
Besides, small and large farms can adopt Lean. Their home farm covers five acres and the couple have a sustainable, profitable operation growing specialty vegetables on less than one acre of land. But the same principles apply to grain and beef farms with mega-sales.
Hartman speaks across the U.S., where the number of farms interested in Lean is booming. He recently held an intensive, two-day Lean startup workshop at his farm and this month is offering new, online Lean Farming courses for farmers who want to learn about Lean from home.
He specializes in helping startup, small-scale farmers get started in Lean, but as above, the principles can be applied to any size of operation.
In fact, the biggest challenge has nothing to do with farm size. It’s whether you can get your head around the concept.
Hartman gets approached for advice by large livestock and grain farmers with tens of thousands of cattle or cropping acres who are excited about Lean and who see the immediate opportunities to implement it on their own operations.
“They see how they can apply it on their farms because waste is universal and it can be eliminated using some very simple techniques,” says Hartman.
That said, he’s passionate about helping smaller-scale farms too.
“I feel that’s the way forward for North American agriculture,” says Hartman, who grew up on a 450-acre corn and soybean farm and believes that the future for agriculture in North America is going to look very different from today.
“For decades we have been stuck in a rut of mass production mostly of corn and soybeans. We’ve saturated the U.S. market and overseas, and we’re struggling to find international markets,” he says. “Now, with counter tariffs from China, it’s another blow… I believe the way forward is to diversify and decentralize our agriculture. Lean offers a beautiful model for how this can happen.”
Get started with Lean
How to get started with Lean on a farm? What are the first steps, and what must be considered?
Hartman’s first step might seem like it should be the last, but he’s adamant. Start, he says, with the end-user or customer.
For farms like his, the fastest-growing new market is in artisanal restaurants, says Hartman. They can offer a great opportunity for an established or new farmer to add an additional, value-added enterprise to their farm.
Hartman suggests a clear path. “Research what are the newest artisan restaurants in a 50-mile radius from your farm and go talk with their chefs,” he suggests. “Identify the value, which means what are they putting on their menu this year? What can you produce for them that no one else is? When do they want it delivered? How do they want it packaged? What volume do they need?”
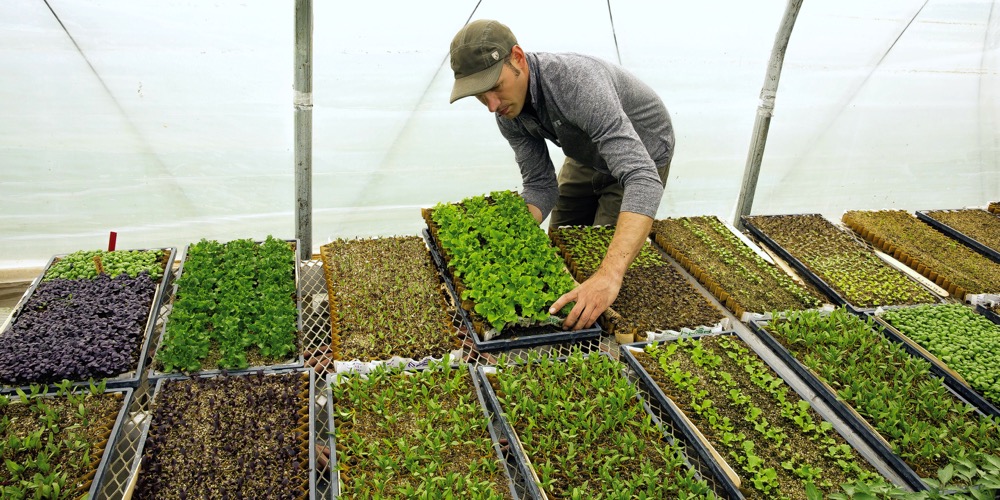
Starting with the customer leads to designing the farm (or a new farm enterprise) to serve that customer. “You might choose to design all areas or just a portion of your farm according to the types of crops that those customers want you to produce,” says Hartman.
Thinking through the farm layout is important, says Hartman, and is something he takes some time discussing in his workshops and courses. At Clay Bottom Farm, a former Amish dairy farm, the couple began by adding greenhouses, converting pastures into vegetable growing areas and turning the former milking parlour into a produce packing room.
On any kind of farm, though, the aim is to keep lines of work straight, short and intuitive. Everything in the system must be designed to allow that flow of work to happen, which in his case involves the ordering and delivery of seed, growth of transplant seedlings in the greenhouses, managing fertility through compost, direct seeding using a precision seeder and organizing the harvesting, packaging and delivery of produce.
Each step is tied to a customer need, Hartman repeats. “The first thing to do is precisely identify value for the customer, because until you have that defined, you don’t know what is and isn’t waste on your farm.”
An eye on market trends
Although a farm obviously can’t change its production system in a minute, the principle is the same, says Hartman. In essence, farms need to be constantly attuned to changes in the marketplace and to trends among consumers and end-users, and to be open and flexible enough to adapt and accommodate change, new ideas and processes.
Clay Bottom Farm has been very good at adapting to change. The farm looks very different today than it did five years ago, growing a very different range of crops as markets have changed.
“Every season we change because our marketplace is very quickly changing,” Hartman says. “Every year 20 per cent more organic fruits and vegetables come from Mexico so the retail availability of organic food has skyrocketed in the last five years. There are massive shifts happening quickly, so we as a farm need to have our ear to the ground, listen to our customers, and more precisely identify value from them… and then change to tightly align our work with the marketplace. That’s the work that any farmer needs to do, but especially these larger commodity crop farms.”
A powerful transition tool
Lean is a tool that Hartman believes can be highly powerful for family farms going through a transition to the next generation. Fresh eyes and new ideas, coupled with the principles of Lean that encourage questioning old paradigms, mean there may be many new and exciting opportunities for new young farmers to develop “leaner” diversified and resilient farm systems.
“If you haven’t inherited thousands of acres of land, big tractors, and access to large commodity-type markets, then you have to Lean up, there’s simply no choice,” says Hartman. “New farmers tend to burn out quickly, and the profit margins are just too thin or non-existent. Lean is all about producing a high-value product and every year lowering your cost of production while increasing the value of your product. It’s a powerful formula for making a sustainable income.”
Learn the five steps
Hartman’s Lean system — which he calls 5S involves five steps: Sort, Set-in-Order, Shine, Standardize, and Sustain.
1. Sort
An early and vital step in developing a Lean system is to take a walk around the farm with a critical eye to begin the process of eliminating waste, which starts with tools and assets on the farm.
“The simplest and most powerful thing you can do is walk around your farm, and for every asset on your farm, ask this question: did it add value for my customer this past growing season?” says Hartman. “If you can say, yes, that’s a powerful tool that produces a lot of value for my customer, you keep it. If you have to question the stuff you use, then that tool should be physically removed from the workplace so you’re not looking at it, tripping over it, it’s not a physical or mental impediment to the flow of your work.”
Hartman does this twice a year, assessing every implement and object on the farm and being ruthless about getting rid of anything that’s not a part of the growing system and does not add value.
2-4. Set in order, Shine and Standardize
Once a farmer has successfully weeded the most obvious tools and assets that are not adding value, the ones that are adding value need to be set in order or organized so that they are most usefully employed and available for the tasks they will perform. Workspaces on the farm should be clean and well lit, Hartman adds, because that allows a farmer or employee to notice when waste is starting to creep into the system.
All procedures and operations on the farm should be standardized so that whoever is performing them is doing them the same way, every time. Hartman, who has one full-time employee and also hires seasonal workers, puts pictures on the wall to visually demonstrate processes and how the products and workplace should look. It’s an easy, timeless way to communicate and has been highly successful at Clay Bottom Farm.
5. Sustain
Probably the last step in the Lean process, but one that’s ongoing, is regularly reviewing and assessing all aspects of the system to try and make it better and ensure it will be sustainable for the long term. Although Hartman and his team are always viewing the farm with an eye to changing or improving things, he does an annual audit every July to assess whether he and Rachel are continuing to move towards the goals they have set for the farm and themselves.
This makes the point that Lean is about Kaizen, a Japanese term for continuous improvement. The idea, says Hartman, is that there will never be a perfect farm: waste will always find a way to creep into the system, but every year there are always ways to chisel it out. The best way to do that is to keep things as simple as possible.
“I am a firm believer that our growing systems can and should become simpler and more intuitive every year,” says Hartman. “As we simplify the system, that decreases complexity in the process and increases what Lean calls velocity (or productivity). We often think we need more complex tools and systems and that complexity leads to productivity. However, it’s usually the opposite on a farm.”
For larger-scale commodity crop farmers, the challenge is also to take a realistic look at options. Should you stay as a grain and oilseed producer, or should you be diversifying, asks Hartman. You can’t know if you don’t investigate it, and if you don’t think in concrete terms about how an alternate production system could work.
You might end up starting to feel as Hartman sometimes feels: “We have a one-trick-pony agricultural system and what’s needed are farms that are able to quickly change what they do.”
He likens this to an industrial process — the Single-Minute Exchange of Die — developed by Toyota engineers who wanted to be able to produce different shapes and sizes of steel parts and to change the dies used to make them within a minute to make their production systems more flexible and responsive to customer needs.
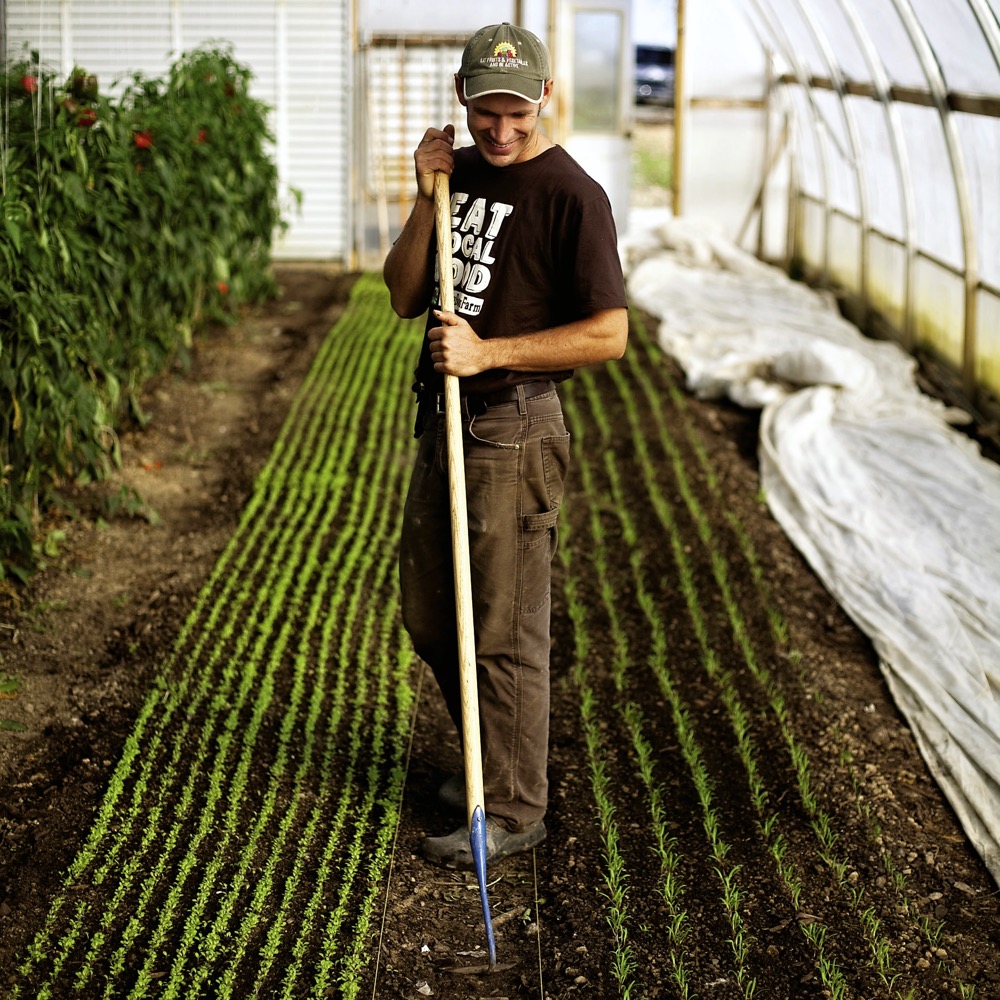