While touring the assembly lines at AGCO’s huge combine and hay-tool plant at Hesston, Kansas, I admit I stopped counting how many workers were greeted by name by Robert Ciecko as he guided our group. But I didn’t stop being impressed by how, at virtually every station, waves came from the workers, or at least a smile and a nod in exchange for his hello.
Those of us on the tour actually looked at each other in amazement a couple of times as the tour neared its end and Ciecko was having yet another brief conversation with a familiar employee.
The guided walk along assembly lines in late March was part of the company’s public celebration of the 100,000th swather to be built at the factory since production began in 1955.
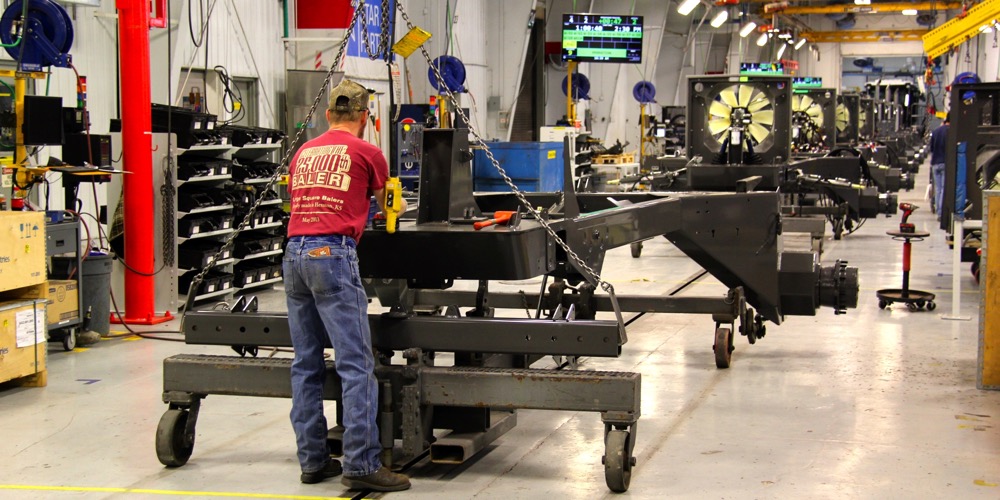
Ciecko is AGCO’s vice-president of Hesston manufacturing. It’s a facility that turns out an average 42 fully completed machines of many types each day, and it’s his job to keep it running smoothly.
Eventually, I just had to ask him how it is that he seemed to personally know nearly every worker by name. I’ve been on lots of factory tours, and I’ve seen lots of managers be friendly with rank-and-file workers. But this was beyond that ordinary, anonymous sort of interaction.
“If you give people respect, you gain respect back,” Ciecko replied in a matter-of-fact way. “It’s the same with customers, management, or the people you manage or work with. I don’t differentiate between operators on the line and people from corporate. I always treat them the same way.”
Read Also
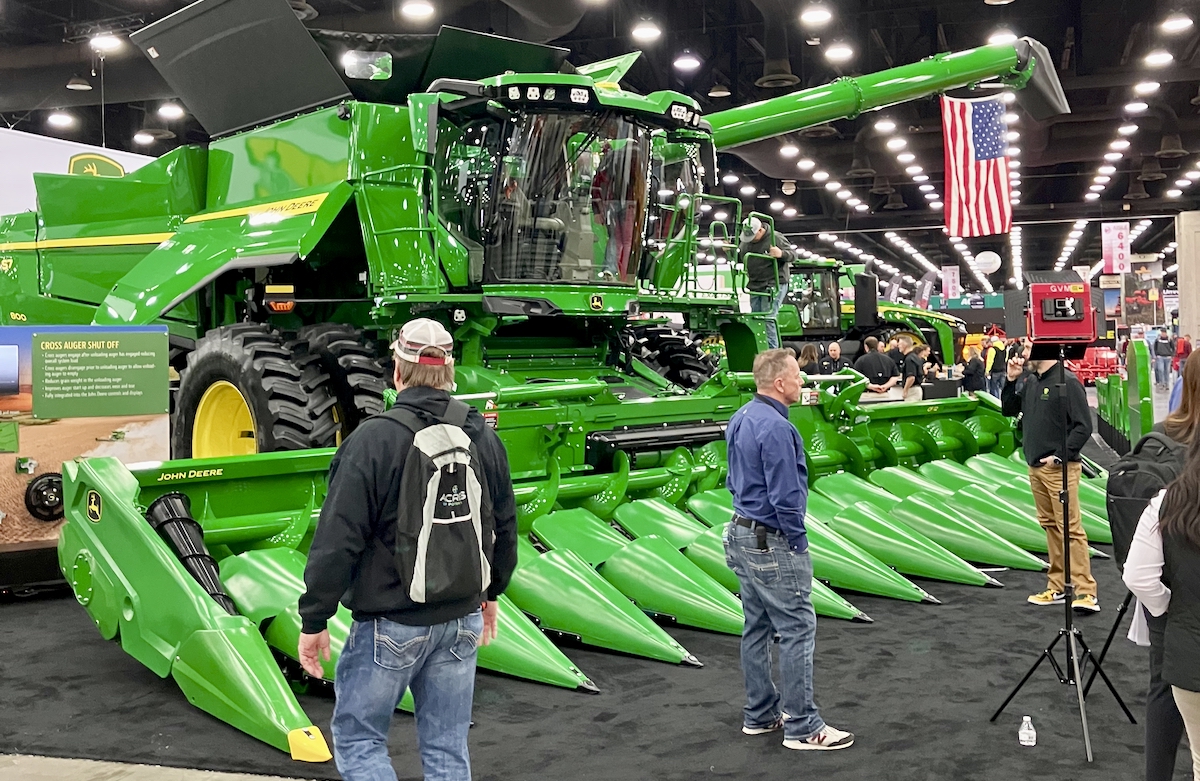
The pros and cons of new technologies
New farm technology hitting the marketplace can be awfully enticing, and it’s not been unheard of in years gone by…
Ciecko grew up on a small farm in Poland, and it seems to have left him with a folksy, unpretentious demeanour. He’s easy to talk to, which may help employees relate to him, and he still has a noticeable accent that hints at his European origin.
But no matter his personal style, a manager isn’t going to know this many assembly line workers by name if he spends the day tucked away in a suite of executive offices in some remote administration building. Only by actually spending time in the heart of the facility can anyone, no matter what their background, come to know staff so well.
So it’s no surprise when I learn Ciecko spends most mornings on the factory floor mingling with the employees who pull wrenches.
“Part of the lean (manufacturing) culture is you spend part of every single day on the floor,” Ciecko told me. “Day-to-day operations are first. Then planning meetings later in the day when I put my thinking cap on. That’s how I structure my day.”
“He’s hands-on,” agreed Christian Ward, a member of the United Steelworkers Union executive at the Hesston plant. “If someone on the line says they need something, he addresses it.”
Ward and another union member were invited by management to join the tour group and chat with visitors.
Like most plant managers, Ciecko is a believer in the “lean manufacturing” concept, which was initially developed by auto manufacturers in Japan a few decades ago. He attributes much of his current management philosophy to learning from previous colleagues and mentors, some of them during his previous tenure at Ford.
Ciecko spent 20 years with Ford, stationed in four different countries and at seven different plants. “There’s always a common denominator,” he said. “People issues are the same everywhere, although this is always something you can learn from each culture.
- See more on Grainews: eQuipTV: Team building at AGCO
“As I grew in the management ranks and had people working for me, I very quickly learned that in order to be successful in a lean manufacturing environment, you need to follow a few very simple rules. One of them is 4M: man, machine, material and method.”
In his own words, this is how Ciecko lives and breathes those four Ms.
Material
“You have to have a basic understanding of the materials that get put together. That makes you a lot more know-ledgeable and helps you understand the issues on the line or design issues.”
Method
“You have to learn the process, which I call method, no matter what you produce, whether it’s trucks, combines, swathers or balers. In other words, you have to have a basic understanding of the materials and the process you use, and how materials are put together.
Machine
“You also need to understand machines, whether it’s simple tools or more complicated electronics or computers to test or aid in the assembly process.”
Man
“Respect for people — I learned it as a youngster growing up on the farm. You have to know your people. You have to know the man. In other words, you have to know what makes operators successful or not.”
Along with celebrating the production milestone that day with customers, media and senior executives, Ciecko and other management staff brought all levels of staff into the event, clearly making them all feel part of the company’s success.
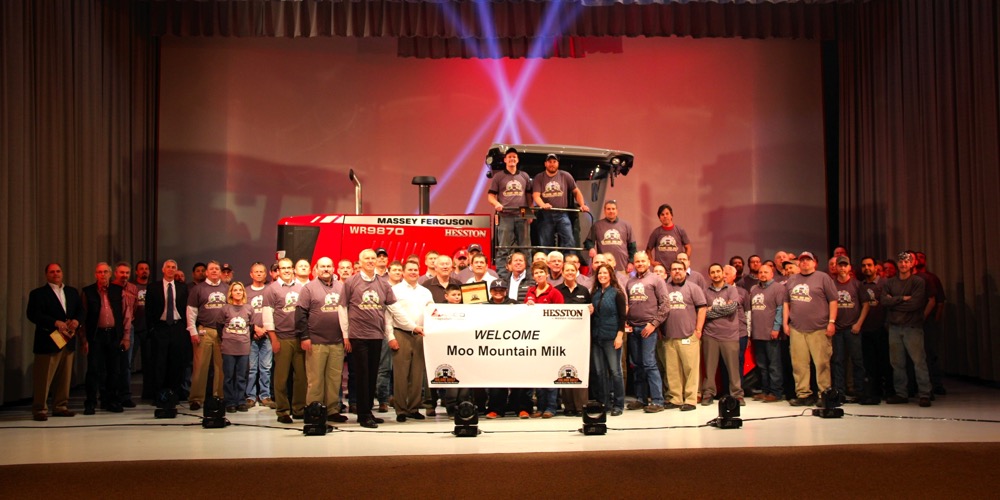
The farm family that had purchased the 100,000th swather was on hand to see their machine revealed for the first time, and it wasn’t just the executives ready to shake their hands. In a first-ever experience for me, the entire assembly line crew was standing outside the auditorium door where the swather was waiting to be unveiled. They shook hands with customers and visitors as they entered, forming a kind of T-shirt-clad receiving line. Then they posed with the customers for a commemorative photo around the swather a few minutes later.
Ciecko and other managers I spoke to all echoed the thought that since the milestone was the result of the efforts of an entire corporate team working toward a common goal, having the rank and file integrated into the ceremony wasn’t only a nice touch, it was essential.
Ciecko had more to say about that.
“I think it’s very beneficial for two purposes,” he said. “No. 1, it’s (beneficial) for employees to see who pays their paycheque. And that is the customer. We, AGCO, simply transfer those funds from the customer in the form of a weekly or bi-weekly paycheque. So it was important to me, and it’s important to every person at Hesston, to see who pays our paycheques. The other one is they (employees) are always curious. I have the privilege of walking people through (the plant) once or twice a week. And they (employees) are always curious. Where do these people come from, what state or what country?”
In today’s labour environment where so many firms, particularly in agriculture, lament that it’s hard to find quality, skilled workers, the inclusive Hesston approach seems to have helped stabilize the plant workforce.
“People tend to stay with us for quite a long time,” Ciecko said. “This is not a revolving door by any means. A lot really grew up on the line. I forgot to mention them as we walked by.”
That last sentence came almost as an apology.
As employees, customers and senior executives all ate a catered lunch together near the milestone machine that day, I spoke more with Ciecko. He summed up the celebration this way: “Days like today make us reflect on the past year, the past decades and how much we’ve progressed, in terms of design, in terms of technology, in terms of efficiency, in terms of quality. It’s a special day. Everyone enjoys it.”