The European model of “lean” farming is a little different from the North American version, and although the primary focus is still eliminating waste, lean takes a more people-focused approach and shares similarities with the principles of holistic management.
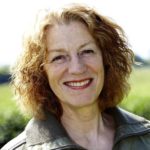
“The lean approach we take is more about management and people,” says Susanne Pejstrup, a Danish farm management consultant who helps farms across Europe, particularly in Scandinavia, adopt lean farming principles.
“The approach we take in Denmark, at least, is that we take small bites, and start with some quick fixes on the farm for quick results, and then continue to educate the farmers in the lean culture, and gradually let the rings spread in the water.”
- Read more: Getting ‘lean’ for farming
It’s also important to identify a leader on the farm who will be committed to the process, says Pejstrup, but it doesn’t necessarily have to be the farm owner. “A farmer may invite us to his farm and he thinks lean is a great project, and we hold workshops and make changes, but after a few months, he will have a new project, so that’s why I need one person on the farm who is going to lead the lean project.”
Read Also
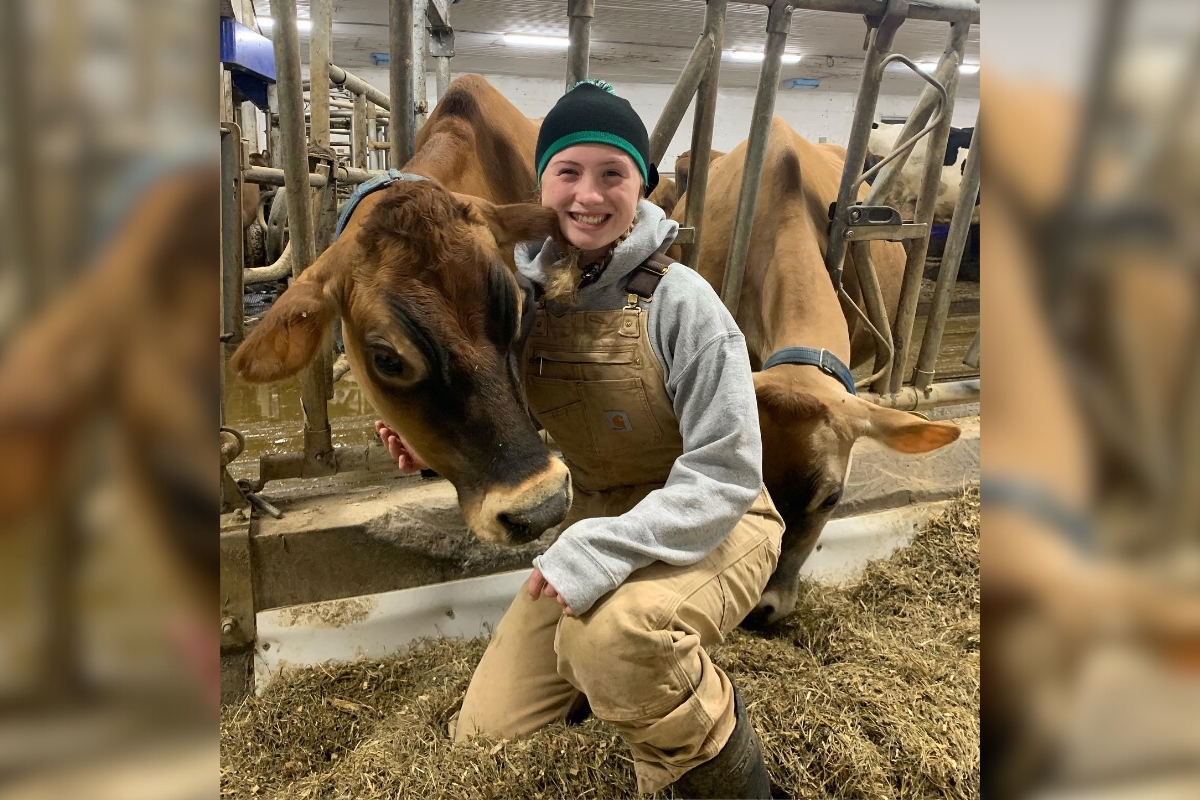
Youth focused on keeping Quebec’s dairy industry strong
In part two of our Making the Future series, Country Guide spoke with Béatrice Neveu from Rawdon, Que. (Read part…
Learning to communicate
Consistency, communication and structure are crucial parts of the lean process, especially on farms, because farmers tend to fly by the seat of their pants a little too much.
“When you’re a farmer, you can have a lot of ideas in your head, and you’re self-employed, and you don’t need to tell them to others, but if you are working with lean you need to talk to others, you need to show them, you need to involve them in how to do things,” says Pejstrup.
“The difficult part with family farms is to be structured enough. They often think it’s ridiculous to stand with a white board and have a 15-minute meeting every Monday morning, and to agree upon what to do that week and to make standards, because we talk to each other every day, they say. But even on family farms, you can see a father, and son, and mother, all do things in three different ways, and they don’t really know how the others are doing it because they never work together. That is another form of waste.”
These procedures and processes need to be standardized, says Pejstrup, but rather than creating written standards that run the risk of ending up on a shelf somewhere collecting dust, the European lean system, similar to Hartman’s, uses a lot of visual cues.
“We have pictures everywhere,” Pejstrup says. “If there is a job where we have four or five steps, we have pictures of each one, and it’s there, where the work is being done, so if someone doesn’t remember how to do something they can check it.”
Interestingly, this visual system seems to prompt ideas and discussions about how to do things differently, and how to improve and standardize procedures. “The people who work on the farm are the ones who know best how to improve it,” says Pejstrup.
High labour costs
Lean farming has become increasingly popular in Denmark, in particular, because over the last 10 to 15 years Danish farms have increased in size, and it’s now rare for the whole family to work on the farm. With more women in the workforce, and farm kids less likely to farm, farm owners have to turn to hired labour to keep things going, and that’s a very expensive proposition in Denmark, where wages are higher than in North America.
It’s why farmers are adopting lean to make them more efficient and to lower costs in other areas and offset the high labour costs.
Lean can be a hard concept for some farmers to get their heads around, admits Pejstrup, largely because they are so focused on production, and not as much on management.
“If you drive a tractor that has too much capacity, and you grow crops that are not the right crops, or have too many animals in the barn so they have lower growth rates and more sickness, it’s not easy to see that as waste,” says Pejstrup. “Sometimes farmers think, I’m here anyway so it doesn’t matter that I work 12 hours a day, but if they could do the job in eight or 10 hours, maybe they could improve their farm. They don’t always see that working ineffectively is another form of waste.”
But after adopting the lean system, farmers continue to make small, incremental improvements that bring them big benefits. Seeing waste becomes almost a passion, Pjestrup says. But the biggest benefit to lean is that, for the most part, they are improving their farm’s profitability without spending any money.