Change can be daunting in any field. When it’s imposed, especially by government regulation, it can get off to an even rockier start, such as with the subject of this article — electronic logging devices (ELDs) and Transport Canada’s implementation of the technology.
Initially, many truckers and fleet operators who have installed the systems were reluctant to use them out of concerns about “someone looking over our shoulders.” Yet in the time since the federal policy was announced in December 2017, most firms and individuals involved in long-haul transportation have responded positively to the change.
Read Also
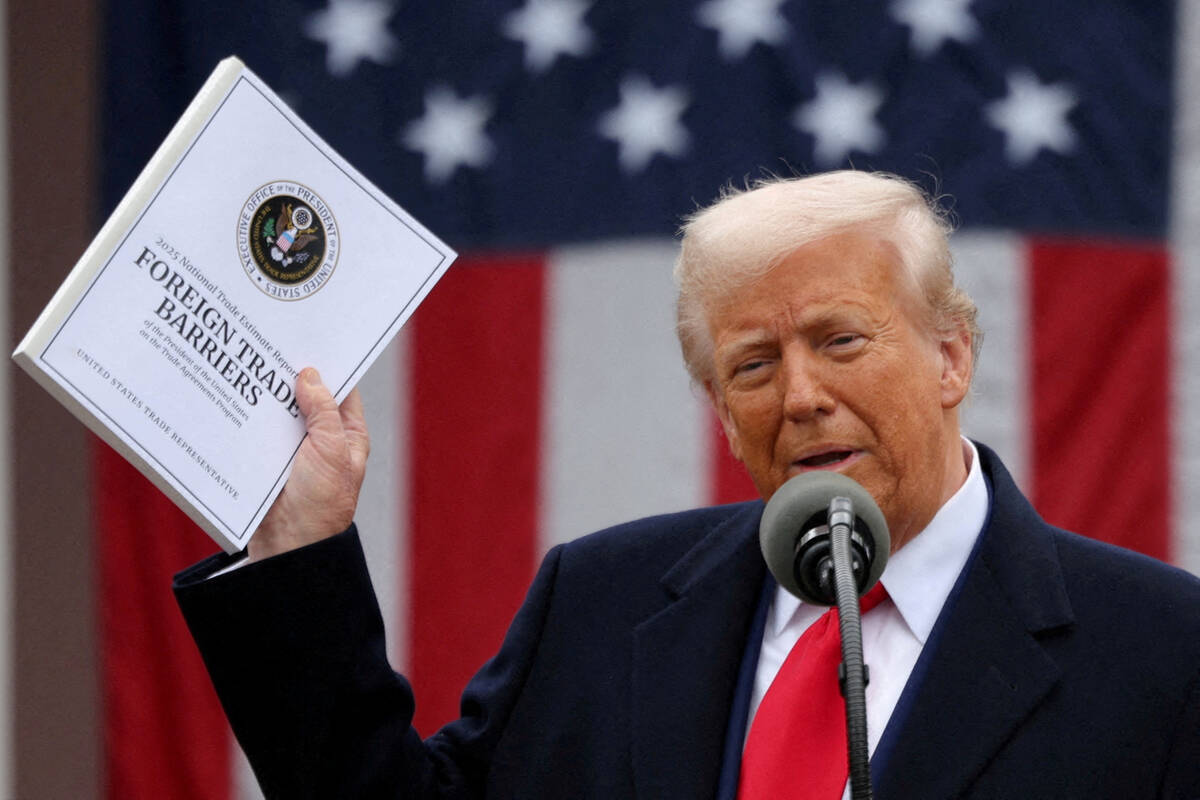
Producers aren’t panicking over tariffs and trade threats
The Manitoba Canola Growers Association (MCGA) surveyed its members this spring to get a sense of how trade uncertainty was…
Canada rolled out its ELD mandate last June with the final date for full implementation set for June 12, 2021. Already, all trucks crossing the border must have an ELD in place to comply with U.S. regulations, which went into effect in December 2017.
Safety first
ELDs are primarily a response to what have been growing issues, especially the falsifying of information and exceeding hours of service. In addition to fines and increased stress on trucks, drivers pushing their limits are often fatigued, causing greater safety concerns.
The cost of installing and maintaining ELDs is another issue that enters into discussions. There are different manufacturers of ELDs with varying price tags but an ELD can cost upwards of $1,000 per unit plus $200 for installation and $60 to $70 for a monthly subscription.
In all, Transport Canada estimates the total cost of implementation at $299 million. But that compares to $380 million in costs for fatigue-related crashes, hours-of-service violations and administrative time, for a savings of $81 million, which doesn’t cover the costs of fines for falsifying log books.
The website ELD Facts estimates that hours-of-service fines totalled more than $15 million in the first month of 2020 alone.
There’s also a time savings associated with ELDs. With conventional pen-and-paper logbooks, notations are made in 15-minute increments. In cases where only five or eight minutes of the next 15-minute block are spent on the road, truckers must “round-up” to the next 15-minute interval, which is why many drivers who switch to ELDs find they actually have more time for driving in a day.
Monitoring a driver’s hours-of-service is also made easier, including the ability to record and report information electronically. An ELD can even tell a fleet manager when the driver has stopped: if they need to call them, they can do so without distracting them at the wheel.
What about agriculture?
In the short term, these new regulations apply to federally regulated trucking firms — loosely termed “fleet carriers.” Farmers who are trucking fertilizer and inputs or harvested crops between depots and elevators and their farms are unlikely to be affected — at least for the time being.
According to “Today’s Trucking”, the rules will change for more than 157,000 drivers who must maintain a log-book for operating beyond a 160-km radius of a base terminal. Long-term, similar rules will be applied to those firms with provincial and interprovincial dealings.
The fallout from the mandating of ELDs has been minimal. Initial concerns about costs of the units or the complexity in their operations have faded among early adopters who have seen better safety standards and improved logistics.
Even so, there are some operational matters to contend with.
“The concerns I’ve heard are that it will cause additional operating costs by requiring more drivers,” says Dan Lefebvre, fleet manager with Co-op Régionale in Verner, Ont. “This would be true if carriers are running with hours-of-service violations. The ELD mandate only strengthens enforcement of service laws that were put in place for public safety.”
Lefebvre adds that for ethical drivers and carriers, the use of ELDs won’t be a problem, but it will force the hand of offenders to make smarter decisions. He notes that he has tested six different providers and found that costs will run between $450 and $750 annually, depending on the features the carrier might require. But he confirms the eldfacts.com statements that the technology can save those costs and more. There are also measures in place for a Power take off (PTO) rebate for auxiliary equipment added to a licensed motor vehicle.
“You can apply to recoup the road tax back for fuel used during PTO operations,” says Lefebvre. “One benefit of the ELD is that some are able to track this for you. Therefore it could cut down on the work that office staff would need to do in order to process the claim.”
The move to ELDs could also help provide digitized metrics to improve logistics, including routing, maintenance planning and engine monitoring. Bruce Crouse, an IoT (Internet of Things) consultant based in North York, Ont., concedes that ELDs might be perceived as one more piece of technology that drivers and companies will be “forced” to implement, but he believes it will ease the administrative workload.
“Haulage drivers will find it harder to double-shift and this in turn will lead to higher infrastructure costs, potentially creating larger driver shortages,” says Crouse, echoing Lefebvre’s statement about hiring more drivers. “But with the focus on carbon footprints and traceability, keeping electronic records is probably something that will be adopted anyway.”
Coming to the farm — eventually
For the time being, farmers are less likely to see any impact, and not just because of the 160-km-radius stipulation in the regulations but because few are fleet drivers. Yet nothing is forever and there may come a time when a grower wants the capabilities that ELDs can provide, such as traceability. According to Ron Campbell, real-time tracking with the devices can provide a number of benefits beyond driver safety or on-road monitoring.
“There’s probably an ability to tack benefits on from ELDs like traceability,” says Campbell, operations and member services manager with the Ontario Agri-Business Association (OABA). He adds that there are many applications where further enhancements — like documenting a truck cleanout — might add value, even if the technology doesn’t exist now. “Every piece of documentation you have from these programs is huge because if you can’t document it, it didn’t happen. The question is: is this a premium or is it access to market?”
With the advent of blockchain technology comes the potential to forge value chains that run direct from grower to retailer. Technology such as ELDs is another step in that development. Campbell agrees that there’s a lot of potential for tracking the movement of food or commodities: ELDs can help track for food safety, showing a load was picked-up at 5:30 a.m. and delivered to the terminal at 8 a.m.
“The biggest value our members see is that the data collected by the ELDs allows for more efficiency in moving product and helps save costs associated with truck maintenance,” says Campbell. “There’s always a challenge with new processes, new equipment, changing the way you do things and having to work with your drivers. But of those I spoke to, no one was against it.”
Further reading: