It is an old axiom but true. The only constant on the farm is change, so each year the management challenge is how to manage that change. Of course, just to make it that much more exciting, we also aren’t allowed to know exactly what the change will be until it happens.
We do have tools, though. We can store grain or we can sell it. And if we decide to store, we can choose whether to pay for commercial space or build bins of our own.
Read Also
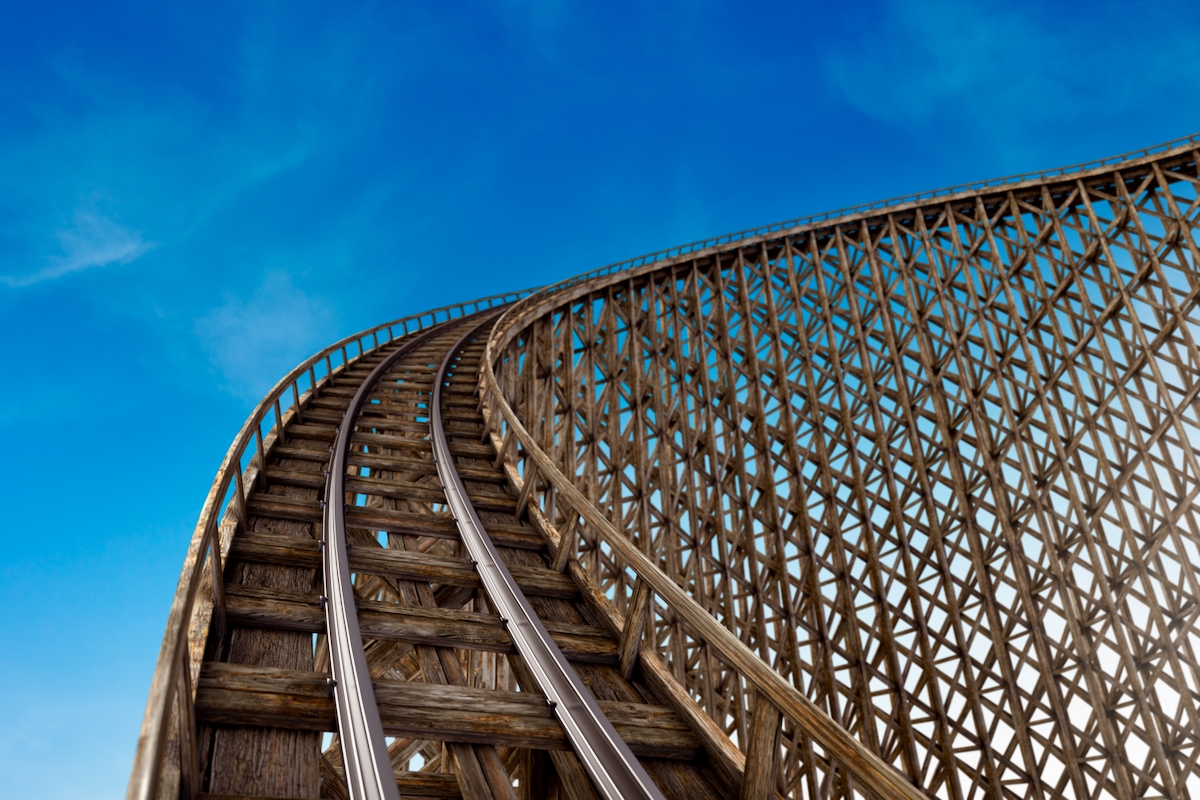
Riding the tariff rollercoaster
Farmers are accustomed to roller-coaster years. But the current geopolitical windstorm is something else entirely. On his cattle operation near…
Such decisions should usually be part of a much larger marketing strategy for the overall farm. But that doesn’t necessarily make them any less complex.
Crop marketing is always one of the greatest challenges for producers, and if you’re looking at storage, you’re actually thinking of changing the interface between you and the market. Inevitably, you will be increasing some of your opportunities, and perhaps taking some others off the table.
For instance, everybody has a different philosophy on the right marketing time to let those crops go. Should we pay commercial storage on those crops or should we build bins to put that crop away for another marketing opportunity down the road?
But that can lead to another question. Just because the bins shine in the early autumn sun, does that mean they should be filled up by default?
There can also be marketing opportunities created by the producer’s ability to control costs associated with storing their own grain. This may be reflected in increased competition for grain off the farm in the off-season or specific value-added opportunities within the marketplace. Key to some of these decisions is measuring and comparing costs between commercial storage and building bins.
You can store grain almost anywhere you feel comfortable. I’ve been there, having dug out improvised storage spaces through the years. However, for this article I got a quote on a 15,000-bushel steel bin with an aeration floor to house wheat, corn or soybeans.
The bin diameter was 33 feet with an eave height of 18 feet. It was equipped with an eight-inch unloading auger, a perforated drying floor, a sweep and a centrifugal fan with a 10-HP engine.
Total cash price for this was $35,062. This included a concrete pad for $5,200 and a labour cost of $3,900.
What wasn’t included in this price was any engineering work, engineering permits, any gravel compaction or further site preparation. Such costs are variable but easily could be in the $2,500 dollar range.
As well, a 200-amp single-phase electrical service would cost from $5,000 to $6,000 to service this bin. As the number of bins increases, the marginal cost of this electrical service would be accordingly less.
In this case the total cost of the bin including the electrical service would be approximately $43,562, although these prices will differ depending on what is ordered and the amount of labour which is needed.
The simple math of putting this bin up is $2.90 a bushel. So when planning for this type of bin construction, payback will come when there is $2.90 per bushel cost savings or higher realized crop prices.
Commercial storage rates can serve as a litmus test when evaluating storage costs. How much does it cost to store 15,000 bushels of grain?
Commercial storage rates for corn were at a rate of 7.0 cents per tonne per day. For soybeans commercial rates were 6.6 cents per tonne per day up until November 1, then a flat rate of $10 per tonne after that until January 1. After January 1 the rate is 7.5 cents per tonne per day. For off-board wheat, the rates are 7.0 cents per tonne per day until the end of August, and after August, $15 per metric tonne.
These commercial storage costs will vary so it is very important to check with your local elevator of choice. These costs also represent a lot of money which could go into on-farm storage facilities.
The questions are, how long do you want to store grain, and why do you want to store it? Is your marketing plan such that you can minimize these costs every year? What exactly are you trying to accomplish by storing grain?
There are many advantages to storing grain on your own farm. For instance, harvest can proceed quickly and to some extent safely versus taking grain out onto the roads. There may also be an opportunity to sell your grain in different value-added markets. One of the greatest paybacks to storage
on the farm is taking advantage of premiums offered after harvest.
Typical premiums for corn into industrial markets can be from 25 cents to 40 cents and sometimes higher depending on the proximity to ethanol plants or specialized feed markets. Soybean premiums for non-GMO soybeans vary on an annual basis, but have ranged from $1 to $2.75 a bushel after harvest over the last few years.
However, when considering a bin, the net premium needs to be considered because sometimes harvest premiums for non-GMO soybeans can be substantial. For instance in this case $2 was the harvest premium with a $2.75 premium after harvest. This would make the net storage premium $0.75 per bushel.
There are many “non-financial” factors to weight when deciding between building storage or sticking with commercial storage, but at a certain point measuring the capital cost outlay is paramount. Using a discount rate which reflects the cost of capital and estimating the present value of the initial cost outlay versus future premium benefits gives a solid financial snapshot of whether one should build a bin or take some other route.
The table represents net premiums available for corn and soybeans and the present value of these premiums discounted at six per cent, reflecting the cost of capital over a 10-year period, the typical amortization period for an on-farm bin.
With an initial estimated cost of $43,562, the table tells us it doesn’t make economic sense based on the net premiums to build that bin for corn at 25 and 35 cent-per-bushel premiums.
For soybeans, it doesn’t make economic sense for a new premium of 25 cents, but 50 cents and higher makes it work.
As a rule of thumb, as the net premium increases, building your own storage makes more sense. A larger discount rate and a longer planning period would surely have an impact on that decision as well.
There is much to consider when answering the question, should I pay commercial storage or build a bin? Part of the answer will deal with how comfortable you are with grain stored on farm versus at the elevator. Part of the answer will also be how your marketing goals align with your storage needs, and part will be pure capital budgeting.
Key will be to settle on a detailed direction for how you want to grow and market your crops. Solid financial rewards may be in the offing. CG