Farms have an impressive record of increasing their production efficiency through scale, scientific improvements and innovation. Efficiency is the ultimate controllable factor in commodity margins.
“Every year we do more with less, better,” says Dick Wittman, Idaho farmer and consultant. “We are becoming safer, more environmentally sound, and more efficient.”
As our farms become more complex and larger, are there opportunities for even bigger gains using formal process improvement?
With more people working on farms, are they following standard operating procedures and are these processes audited and rewarded for improvement?
Farm process improvement should define your company’s culture, says Wittman.
In the manufacturing sector, management programs like Total Quality Management (TQM), lean manufacturing and Six Sigma are being implemented to ensure quality and margins. Measuring and knowing how often the process varies from the standard is key to improving. For example, for Six Sigma, the sigma rating states the yield or the percentage of defect-free products it creates. In a “six sigma” process there’s likely to be only 3.4 defects per million, for a free-of-defects rate of 99.99966 per cent.
In Canada, Larry Martin teaches lean management at Canadian Food and Agri-Business Management Excellence (CFAME). Those in the CFAME course say it’s slower than expected to implement and needs a cultural change to happen effectively, says Martin’s business partner, Heather Broughton. “We also thought the concept could be applied into primary agriculture, so we have brought the content into CTEAM as well the last couple of years,” she says.
Read Also
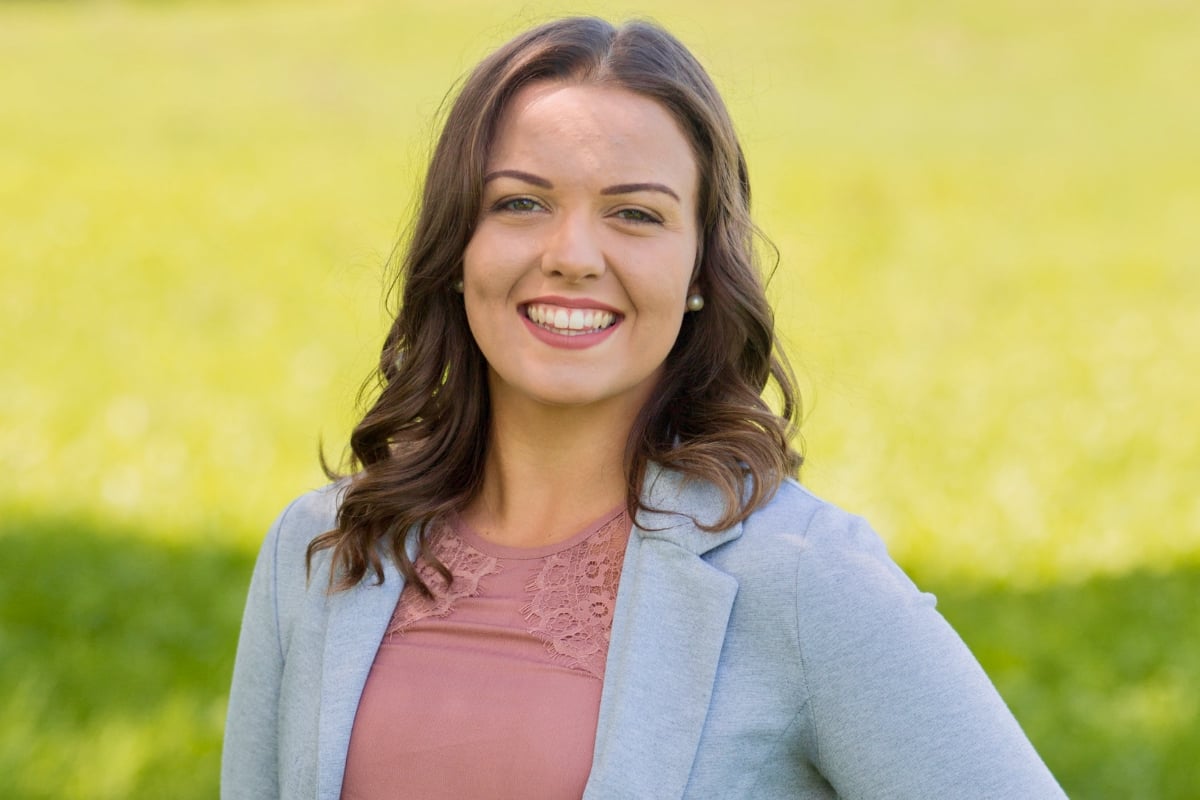
Youth motivated to find answers to today’s agricultural challenges
This is the first in a series of articles exploring the perspectives and experiences of young people who are finding…
Whether it’s TQM or Six Sigma, all these programs have two common threads — process mapping and developing standard operating procedures.
Wittman teaches process improvement at Texas A&M University’s The Executive Program for Agricultural Producers (TEPAP), with a stress on developing standard operating procedures. At the beginning of the course, he points out the vulnerabilities farmers carry in their businesses that could be mitigated with improved, more formal processes. Stories include not having any backup systems when computers crash, but also large fines levied for environmental problems or key employees quitting and no one knowing how to do their job.
Then Witttman literally takes it home. He tells of how one of the partners on his large, diversified family farm was severely injured when he rolled a tractor. The roll bar had been removed to clean out a building, one tire had been repaired but the liquid calcium hadn’t been replaced yet and he was driving on a hill. In that instant when that tractor rolled and crushed him, having standards to follow went from being peripheral to imperative. “We preached and practised farm safety but having it orally wasn’t enough,” says Wittman.
The next morning, all the employees and partners at Wittman’s farm sat down and reviewed everything. Then they immediately started creating a six-page safety policy for the farm, writing down everything from chaining down a tractor to putting the roll bars back on after cleaning out the barn. Today, new employees sign that document and take a copy home to read.
Written safety policies can act like the mortar for standard operating procedures (SOPs). They should get everyone on the farm up to speed with awareness, and they can also help prove due diligence should something bad happen.
However, the benefits of improved processes go beyond risk mitigation. In fact, it’s the cost of things going wrong that motivates many TEPAP participants to spend the time developing SOPs and then improve on them, says Wittman. Plus, there are the benefits of superior planning.
Huge savings can be realized when efficiencies are identified, evaluated and implemented. “This is the highest payback for management and time,” says Wittman.
Part of the resistance is just in our personalities. “Farmers like to grow stuff, not put things in writing,” says Wittman. But that is changing. This year 40 per cent of the TEPAP class had personality and communication styles that were focused on processes, and Wittman says they were eager to get home and write SOPs.
Process improvement for farmers starts by identifying jobs that are repetitive, documenting how those jobs are supposed to be performed, and evaluating how to do them in a ways that are better, more efficient, safer, more economical and more environmentally sustainable. Then, the process ensures you audit how you are doing, and reward the gains that result.
“Success is doing things well over and over consistently,” says Wittman. “Be a courageous leader in being alert to deviations, and take responsibility for adherence to standards.”
Once identified, the cost of inefficiency should be analyzed, because now there’s a marker to measure the improvement. For example, in the TEPAP course, Wittman goes through an analysis of how many years of payback it would take to move from 40-foot trailers to grain trains. When the steps were broken down, the problem of combines waiting around was identified and valued. Replacing trailers with grain trains becomes quantifiable.
But process improvement doesn’t stop with a calculator. Alternative solutions are identified and the best one is implemented after looking at the total picture and implications. The new process is evaluated to ensure this was a good move and seeing how it can be improved further. It’s a very engaged, fluid and continual process.
The power comes when each product or process is evaluated based on its ability to streamline an operation, increase production, improve quality or save time. It starts by breaking down what happens currently and then really looking at these processes as a way to improve. For example, simply putting a label on something can help avoid making the same mistake over and over. It might help eliminate duplications, extra steps and inefficiencies.
What’s an SOP?
Standard operating procedures (SOPs) describe the steps and the order of actions to complete a process, such as milking, planting or spraying. These steps are the links in the chain that make up the process. They don’t necessarily have to be written. Some of the best SOPs are video recorded. With smart phones and YouTube, this can be done quickly and inexpensively. “Some large dairies are doing this (video SOPs) in a second language for some of their employees,” says Wittman.
Typically, SOPs are used to train new employees, to do performance reviews and job descriptions. Often employees write their own SOPs, which can then be used in performance evaluations to help isolate problems or verify environmental safety.
On all sizes of farms, they’re a great way to remember how to do tasks that only get done occasionally, and can be used as a checklist for rewards and consequences. Like the standards of Six Sigma, they should reduce variability and errors.
When Wittman’s daughter went off to college, it left their farm with no one who knew how to do billing and other office duties. His youngest child, then eight years old was keen to learn, so he described to her the task while he was doing it and she wrote it down. By the end of several sessions like this, she understood the job and the farm had clear easy-to-understand written instructions for office duties.
To make them even more useful, they should be measured and used on a day-to-day basis, says Wittman. And at least once a year, they should be reviewed and updated. Process management isn’t just a one-time thing. Also, don’t become bound by your standard operating procedures; that’s not the point.
Wittman identifies eight farm applications of SOPs:
- Office functions
- Harvest and equipment operations and servicing
- Crop agronomic practices
- Fuel and farm supply and storage
- Worker safety guidelines
- Food safety practices
- Herd health and stock-handling procedures
- Value-added market access and certification
Think about your own farm and where you could apply some standard ways of operating. Then, prioritize which ones need to be done first. For example, equipment maintenance checklists might be a good place to start. Then you could move on to written operating instructions for key equipment, as well as shop protocols for jobs like replacing used products or prepping equipment for field work.
You could also tackle seasonal work-flow planning, beginning with markers and white boards, and then developing a more formal approach including, for instance, how to do harvest-crew orientation, how to manage on-farm grain storage, and how to check bins after the grain is stored.
Process management begins with “process mapping,” or defining what the business does and who is responsible for what. Once a process is outlined, then it’s natural to look for ways to make it more efficient. It also can be used to help determine when it makes sense to invest in a new product or technology.
It also might make sense to talk about process improvement with your supply chain. For example, sharing your feeding SOPs with your nutritionist might identify a problem or another way of doing things that you didn’t even know about.
Having processes written down might give you a leg up for selling into premium markets, especially because you can demonstrate to buyers that you are on top of everything that happens on your farm.
In a related way, SOPs can also help prove that your are in compliance for things like animal care or environmental standards.
As Wittman says, breaking down the steps in process, could be the start of squeezing more time and margins out of your farm. But that in itself may be only the start.
This article first appeared as ‘Farm P.I.’ in the March 17, 2015 issue of Country Guide