Precision agriculture just keeps getting more and more precise. The industry has seen the advent and refinement of yield monitors and variable-rate application, and now it has moved on to improved singulation in planters, automated down-pressure, and higher planting speeds.
Most of those innovations have come in response to a growing time crunch. The windows for planting, spraying and harvesting are getting smaller and tighter, partly due to climatic challenges in the past few years, but also in response to the trends toward expanded farm acreages and the size and complexity of operations.
Read Also
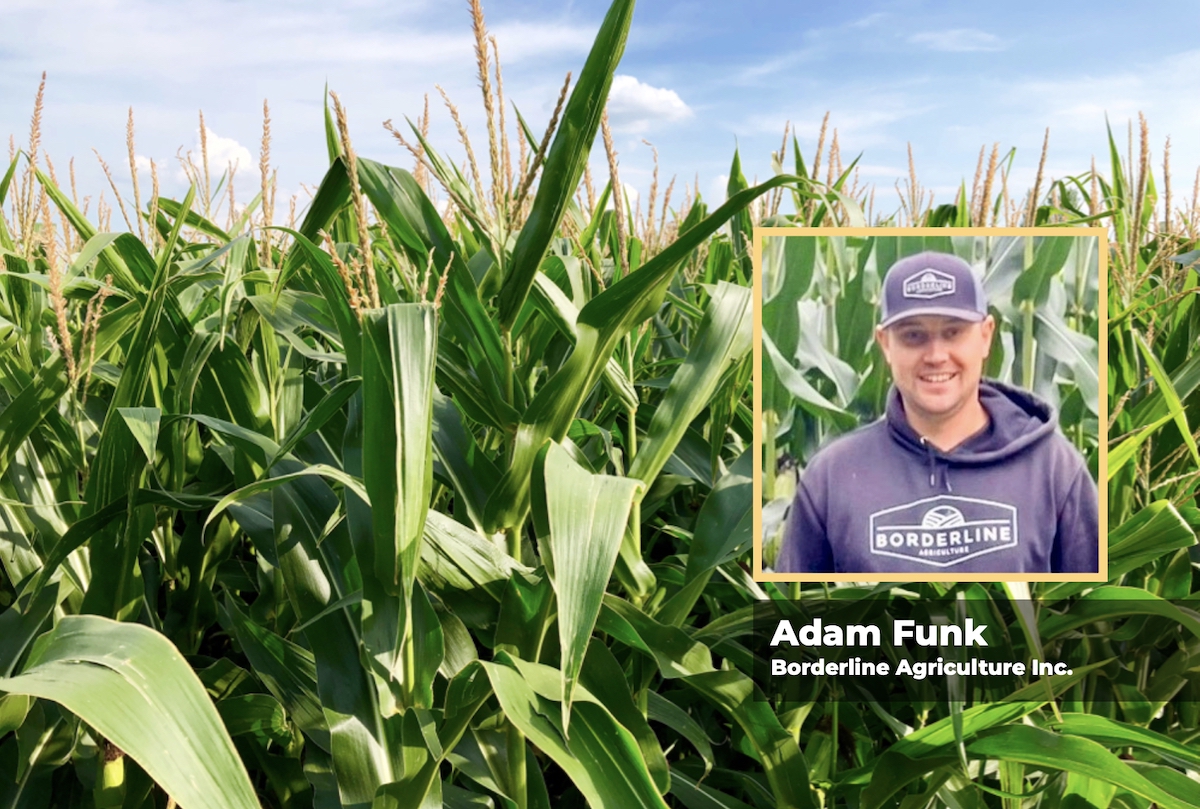
Agronomists share tips for evaluating new crop products and tech: Pt. 3
With new products, new production practices and new technology converging on the agriculture industry at a frenetic pace in recent…
Now there’s a newer technology for increasing efficiency for growers and for those with significant contours on their land.
Electric seed meters have been around for about three years. It was 2011 when Graham Equipment first entered the market, and since then, Horsch has made the technology standard on its units while Kinze is adding them to the latest upgrades on its 4900 series planter. Precision Planting is also adding after-market kits (similar to Graham’s). And last August, Case IH announced it would provide growers with the option of having Precision Planting electric meters installed directly at the factory.
For the proponents of electric metering technology, the advantages are numerous and far ranging. One, the move towards widespread adoption of electronics is already taking shape. Two, in terms that are specific to planting technology, electric meters remove the clutches, chains and shafts of conventional systems. Three, singulation is a much simpler matter, given the meter’s ability to handle any seed size or shape or even speed. And the plant spacing, no matter the curves or contours, is kept constant, which, says Tom Snyder, is a huge benefit.
“Our whole challenge in the industry is to get a meter that will properly singulate and distribute seed across a wide variety of sizes and shapes,” says Snyder, owner of Grand River Planters in Caledonia, Ont. “If we go around contours with the planter with the electric drives, every meter turns at the rate it needs to keep your spacing consistent, whereas with a shaft-type system, that whole shaft turns at the same speed. It doesn’t matter if the planter is going straight or around a contour, so you can end up with overpopulation on the inside rows and underpopulation on the outside rows. And it costs you money.”
But that doesn’t happen with electric seed meters.
Now, more farmers are agreeing that if technology can save them from physically getting in and out of the tractor cab, or if it ensures correct spacing, it has to be worth something. With the Precision Planting unit, the electric drive system — the eDrive — is designed to work only with the company’s vSet meter. That, says Snyder, allows for the installation on almost any manufacturer’s planter. As long as the seed tube can be lined up on the meter, everything should work without any problems.
Admittedly, there’s some issue with so-called “sticker shock,” and Snyder concedes there may be some reluctance to invest that money in this technology. But in comparing the two types, Snyder points out that adding end-row shut-off clutches and hydraulic drives for variable-rate technology also adds to the price of conventional seed meters and planter setups. Once those add-ons are taken into consideration, the pricing discrepancy isn’t so wide, he argues. Plus the trend is favouring the move towards electronics in seed meters; in a few years, it’s expected that electric meters will become the standard.
“When you think about electronics and what we can gain as far as the torque of an electric motor over and above what a diesel does running through an engine, it’s huge,” says Snyder. “It might not come as fast as what some want, but there are definitely advantages to it. We’ve tried them on our own farm and we’ve made a lot of improvements on our own planter. There are a few things I just wouldn’t budge on, and one is that I wouldn’t go back to a shaft and chain-type scenario; electric drives are where it’s at.”
Electric has its place, but…
For Kirk Van Will, electric meters may be the way of the future, but for now he sees a limited uptake in the technology in his immediate area. As a yield specialist for Lambton and West Middlesex counties for Maizex Seed, he admits his experience with electric metering is limited. He does recognize the advantages in relation to time saved in mechanical maintenance and repairs, not to mention the ease of operation, especially as the trend in expanding acreages continues.
“If you look at farming today, there are more of the larger farms, which indicates a grower is becoming more of a manager, or at the very least, someone who’s not quite as hands on,” says Van Will, who’s based in Strathroy, Ont. With electric metering, he says, “the hired employees they have don’t need to worry about all of those clutches that take time to learn. This is more of a snap-it-in system, and away you go.”
The advantages to Van Will are obvious. Beyond the time savings for learning and repairs of conventional planter technology, there are the contouring capabilities, matching turns with row spacing requirements. That may not be a huge factor for a region like Lambton, where a lot of fields are squared off. But in regions where a stream meanders through a field, or a tree lot isn’t squared to the property line, this technology is more likely to gain acceptance.
Yet Van Will maintains that the technology’s marketability will be challenged by certain current realities. For instance, those growers who are mechanically inclined and are capable of working with chains, clutches and hydraulics may not be as quick to change. The counter to that may be that growers are beginning to understand the value of their time. They may be able to fix things themselves, but in recognizing how and where to better spend their time, they may feel they’re better off with a new planter and electric seed meters.
Another factor that could slow acceptance is in diagnosing any problems. Snyder concedes that loss of the alternator on an electric meter would create significant headaches for a grower, especially in the middle of planting season. But Van Will takes that one step further — to the machine’s downtime.
“Running wires along the frame of a planter and by row can be problematic,” he says. “And when you store it in the winter, there are rodents and other pests that can get in there. Then you have a grounding wire touching a frame or it gets worn and touches a frame, it can really create a lot of havoc.”
In order to avoid those issues, a grower might just choose to rewire the whole system.
Still, there’s a tone of inevitability that Van Will agrees is hard to counter: the trend is already taking shape, and electronics will become the new standard. Even those growers who have recently purchased a new planter will reach the point in the next five years when the technology has become more widely adopted and prices have come down because of the availability of the technology.
At that point, it’d be a little easier for the grower to make the decision to move to an electric-metered system.
“I would wonder if you won’t see those electric meters start to pop up just because of that,” says Van Will.
It’s not really a matter of electric seed meters increasing final yields. Much like unmanned aerial vehicles (UAVs) or electronic soil analysis, the technology alone does not make a farmer better simply by owning or utilizing it. It only increases efficiency in the hands of a knowledgeable user.
Increased yield still comes down to what’s in the seed, how it’s planted and how it performs in the field. Technology, however, can improve efficiency, and on more farms today, efficiency is getting to be a bigger and bigger deal.