A complete set of wrenches seems as essential to farming as owning a tractor. Skinned knuckles from using them is proof you work smart. But, asks Michael Bevans (above left), is your shop actually good for your business?
Why ask dumb questions? Of course doing your own maintenance and repairs makes you a better farmer. How could it possibly be cheaper to pay someone else to do something you can do?
Well, lets put the numbers to the test. But be prepared. It won’t be as simple as you might think. Like everything else in farming, finding the least-cost option for machinery maintenance and repair involves evaluating a lot of alternatives.
Read Also
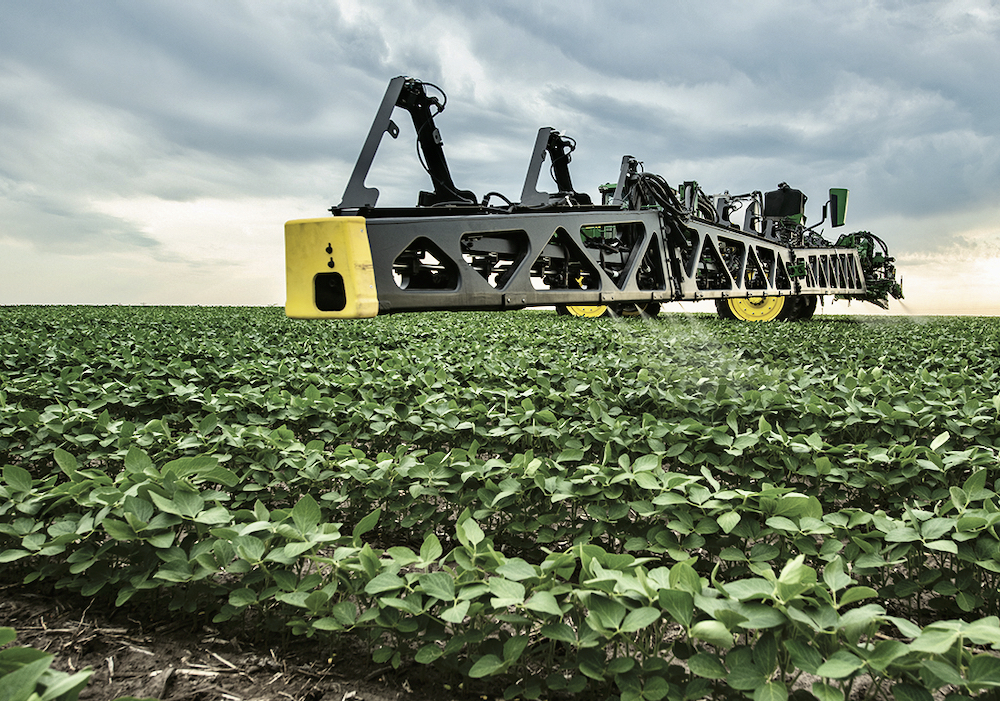
Farm machinery scores big in 2022
When I spent a summer working as a mechanic’s helper at an Allis Chalmers dealership in 1978 as one of…
Lets start with the farm workshop. Every farmer sometimes finds them-self lying on their back in crop stubble, struggling to make an in-field repair despite the dust and the grunge dropping into your eyes.
Most serious repair work, however, needs to happen in a controlled environment. Hence the need for a farm shop if the work is going to be a do-it-yourself project — as it often is.
It seems natural to assume that every farmyard needs a workshop. If there’s ever any question about it, it’s a question about what tools you need, or how much bigger you need to make that door.
Think about it, though. Those questions can have awfully big implications.
A Properly Maintained Engine Should Go 6,400 Hours Of Operation Before Needing An Overhaul. Yet The Average Tractor Engine On A Canadian Farm Lasts Less Than 4,000
Today’s farm machines are big and they’re getting bigger, and that means the farm shop has to keep pace. But how big is big enough? When I put that question to the instructors at Assiniboine Community College’s School of Trades and Technology (ACC) in Brandon, Man., the general consensus was that 5,000 square feet would be ideal. At a minimum, it needs to be 3,750 square feet. And those walls should be 18 feet high, although 20 would be better.
Why so big? In a word, combines. These maintenance hogs are becoming giants, and you still need room to work around them once they’re inside. A four-wheel drive tractor with duals eats up a lot of space too, and don’t forget, the shop also has to include room for workbenches and large tools like a hydraulic press and welder, among others. Plus you needs shelves and cupboards, and someplace to store oil and parts… well, the list goes on and on.
According to Trevor Hicks, a partner at Goodon Industries, a Manitoba-based farm-building contractor, producers are recognizing this need for more space in their workshops. His company now frequently gets orders for farm shops of 3,600 square feet and larger.
A bare-walls building of that size will cost about $120,000, Hicks says, working out to just over $33 per square foot. Then you need to stock it with tools, and you need heat it and pay for the electricity.
All things considered, a lump of cash that size can buy quite a bit of work at a professional service department. For small producers, it might cover most or all the repair work they will ever need, including having a dealer send out a mobile repair truck for in-field breakdowns.
While a shop filled with tools amounts to some serious on-farm investment, Michael Bevans, a project manager at the Alberta Ag Tech Centre, believes calculating the farm shop cost into the equation may not be fair.
“It’s tough to assume the cost of the shop,” Bevans says. “Most farms are already going to have one.” Although it may not be 5,000 square feet, making use of whatever buildings exist is just being sensible. And the shop can also be used for off-season machinery storage.
But, Bevans says, the cost of equipping a shop with many of the tools necessary to work on modern equipment is a factor that’s worth thinking about. Even if you spring for that investment — which can run well into the thousands — you still need to know how to use them.
Back To School
Brett Callin, a student in ACC’s Heavy Duty Equipment Technology program, thinks learning how to use those tools by taking mechanical training is something farmers ought to consider. “When you think about it, $5,000 for an education that can save you thousands in the long run is a pretty darn good investment,” Callin says. And he isn’t alone in thinking that way.
Marty Zuzens, an instructor at ACC, says the number of students now taking mechanical training for their own use is growing. “In the last few years we have seen a large increase in students taking our program just to improve their mechanical skills and return back home to farm,” Zuzens says. “Where the ratio before was one or two out of 15, now we are seeing three or four.”
Callin also sees other opportunities to make his mechanical expertise pay off. “In the winter time, when things slow down, there is always tinkering around to do,” he says. “And if you have a big enough place to do it in, you can make a little money on the side.”
Rodney Verway, another student in ACC’s technical program, agrees. “(In) the winter months when things slow down, there is no reason servicing the combines or grain trucks and other equipment can’t be done,” Verway says.
The mechanical ability Callin and Verway are picking up by going to college may be more important now than ever. The equipment coming out of farm machinery factories these days is so technically sophisticated, dealers are sometimes getting told they won’t even be allowed to sell the new machines unless they have technicians specifically trained to service them.
Self-propelled, high-clearance sprayers are an example. Some manufacturers have limited sprayer sales to a select group of dealers with the necessary expertise to handle them. The writing on the wall is that for most farmers, this is equipment that you may not want to take a wrench to. In fact, diagnosing the problem may not even be possible without the proprietary computer software some manufacturers only make available to authorized dealers.
Bevans says the farm-machinery repair sector is currently going through what the automotive sector did a few years ago, where smaller, independent repair shops can no longer access the necessary computers and software needed to troubleshoot some systems. “When you get into certain problems you are going to have to call the dealer because of their ability to hook up to a computer,” Bevans says.
Despite that, he says, the demand for independent mechanics doesn’t seem to have waned. Their ability to work at considerably less than dealers’ shop rates may be the reason. Dealership service rates are now hovering around the $100-per-hour range in many regions. An independent mechanic can often work much cheaper, particularly if they can do the job inside a farmer’s own workshop.
“They’re becoming more popular with the guys that don’t have full-time staff,” says Bevans. “Some
Back To School
Brett Callin, a student in ACC’s Heavy Duty Equipment Technology program, thinks learning how to use those tools by taking mechanical training is something farmers ought to consider. “When you think about it, $5,000 for an education that can save you thousands in the long run is a pretty darn good investment,” Callin says. And he isn’t alone in thinking that way.
Marty Zuzens, an instructor at ACC, says the number of students now taking mechanical training for their own use is growing. “In the last few years we have seen a large increase in students taking our program just to improve their mechanical skills and return back home to farm,” Zuzens says. “Where the ratio before was one or two out of 15, now we are seeing three or four.”
Callin also sees other opportunities to make his mechanical expertise pay off. “In the winter time, when things slow down, there is always tinkering around to do,” he says. “And if you have a big enough place to do it in, you can make a little money on the side.”
Rodney Verway, another student in ACC’s technical program, agrees. “(In) the winter months when things slow down, there is no reason servicing the combines or grain trucks and other equipment can’t be done,” Verway says.
The mechanical ability Callin and Verway are picking up by going to college may be more important now than ever. The equipment coming out of farm machinery factories these days is so technically sophisticated, dealers are sometimes getting told they won’t even be allowed to sell the new machines unless they have technicians specifically trained to service them.
Self-propelled, high-clearance sprayers are an example. Some manufacturers have limited sprayer sales to a select group of dealers with the necessary expertise to handle them. The writing on the wall is that for most farmers, this is equipment that you may not want to take a wrench to. In fact, diagnosing the problem may not even be possible without the proprietary computer software some manufacturers only make available to authorized dealers.
Bevans says the farm-machinery repair sector is currently going through what the automotive sector did a few years ago, where smaller, independent repair shops can no longer access the necessary computers and software needed to troubleshoot some systems. “When you get into certain problems you are going to have to call the dealer because of their ability to hook up to a computer,” Bevans says.
Despite that, he says, the demand for independent mechanics doesn’t seem to have waned. Their ability to work at considerably less than dealers’ shop rates may be the reason. Dealership service rates are now hovering around the $100-per-hour range in many regions. An independent mechanic can often work much cheaper, particularly if they can do the job inside a farmer’s own workshop.
“They’re becoming more popular with the guys that don’t have full-time staff,” says Bevans. “Some