Pre-separation boosts Lexion efficiency
The Lexion 500 Series rotary and straw walker models are designed to boost both harvest and fuel efficiency with an award-winning threshing and separation design. The Class IX 595R / 590R and other 500 Series rotary models feature the Lexion Hybrid System, a combination of conventional threshing cylinder technology and a dual rotary separation system. It starts with the accelerated pre-separation system (APS) which includes the accelerated pre-separation cylinder, a main threshing cylinder and an impeller.
According to Claas, up to 30 per cent of the grain is separated at the APS cylinder and sent directly onto the cleaning system. The remaining crop is fed into the main threshing cylinder at a gradual angle, covering the entire width of the cylinder at a constant thickness, which results in higher grain quality. The impeller then divides and feeds the thrashed material into the RotoPlus dual rotary separation system.
Read Also
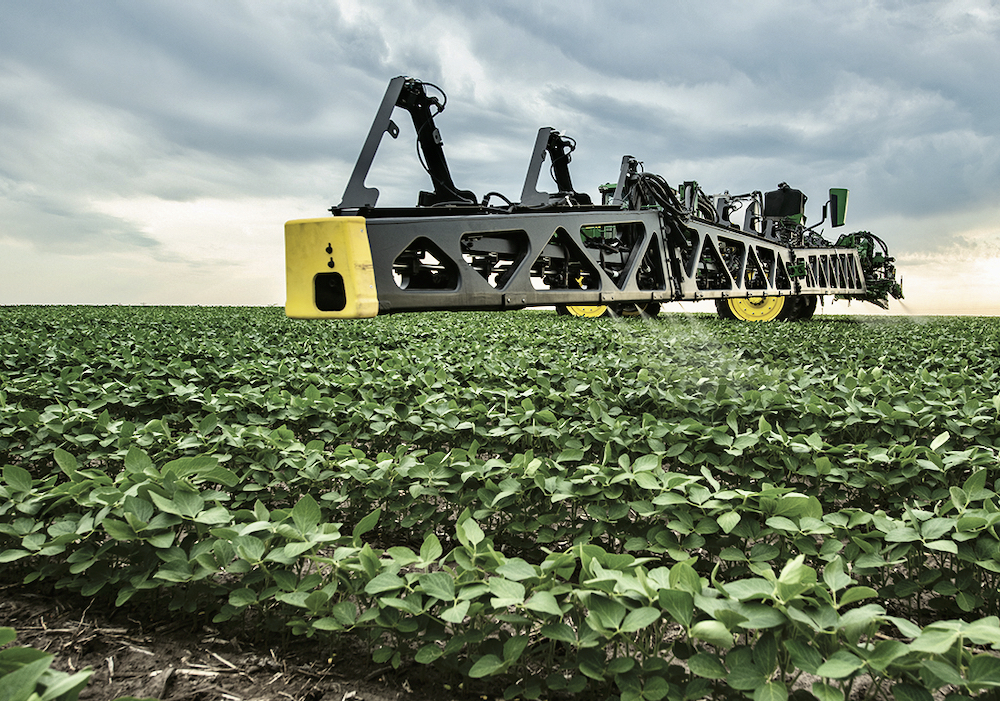
Farm machinery scores big in 2022
When I spent a summer working as a mechanic’s helper at an Allis Chalmers dealership in 1978 as one of…
The dual rotors are smaller (17.5 inches) and longer (14 ft.) than traditional single-rotor combines. These rotors generate greater centrifugal force, which the company says translates into better separation with increased efficiency and capacity while decreasing the power requirements for greater fuel efficiency.
The Lexion 570 walker combine features the walker separation system. First, the impeller spreads the crop mat across the entire width of the straw walker. Then the Multi-Finger Separation System, which consists of a rotating drum fitted with retractable tines, fluffs and agitates the straw, increasing grain separation in the straw walkers and making it easier to separate the remaining grain from straw.
Hydrostatic rotor the heart of AGCO design
The largest ACGO combines in the Gleaner, Massey Ferguson and Challenger lines all boast the same large 800-mm diameter, 3.55-metre long rotor, which is hydrostatically driven and allows the operator to harvest at a constant rotor speed. It is also reversible, with a three-speed gearbox that is designed to allow an optimum speed range and increased torque to handle the crop efficiently.
The rotor has four main sections: intake, threshing, separation and discharge. The crop is fed into the rotor through a full-width helically vaned beater, which sends it 360 degrees into the threshing area. A stone trap is located immediately below the front beater.
The concave contains three sections with nine “bolt in” concave modules. According to Challenger, the threshing elements are coated with tungsten carbide and the rasp bars are chromed for longer life. Three rows of seven rotor knives are bolted to the entire length of the rotor to increase efficiency by keeping the threshed mat broken up. There is no rear beater. Challenger says that with a rotor of this size, none is needed; straw can be directed into a swath or put into a min-till chopper.
www.challenger-ag.com/www.masseyferguson.com/agco/mf/na/www.agcoiron.com