In precision agriculture, there can be a steep learning curve with the newest systems on the market. Planter clutches and variable-rate fertilizer systems have their intricacies, for instance, and it can take growers years to customize key components to fit their particular operations. Now, however, there may be help, based on a connectivity technology that overcomes bottlenecks using data management. Although the concept isn’t exactly new, this ability to tap the power of the Cloud definitely is.
Controller area network (CAN) bus systems originated in the automotive industry, enabling multiple controllers to operate and exchange information tied into a single circuit or “bus.” It’s the same system that made it possible for a mechanic to read a car’s diagnostic fault codes, or for a driver to raise all four windows at once.
Read Also
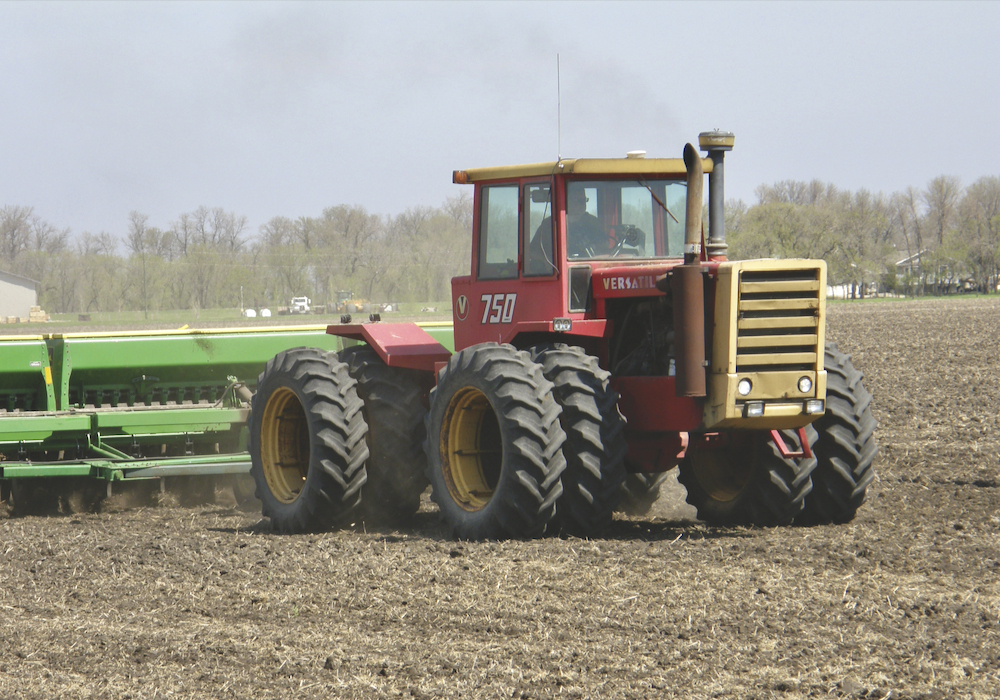
Summer Series: Old machines,new technology
One of my first jobs was working as a mechanic’s helper at a farm equipment dealership in the late 1970s….
It has also been a part of tractor technology for a decade, replacing wire boxes, harnesses and the tangle of wires necessary for one machine to “talk” to another.
Despite not being new, however, the CAN bus system was cited in April 2013 as one of many technologies that are changing agriculture.
“With CAN bus, everything essentially travels on two wires, so we’re all on the same network and everything can talk to everything else,” says Ben Craker, senior global marketing specialist with AGCO. “If you look at connectors for implements today, there might be seven or eight different wires in the implement plug going to the tractor, and there might be three or four going from the terminal on the machine into the wiring harness, and that’s just because there’s generally two different networks on the machine where all of the communications are going on.”
Just as a mechanic can read diagnostic fault codes on a car, farm machinery mechanics can now do the same with a tractor, thanks to CAN bus technology. But the system also provides the opportunity to glean much more, such as data on fuel consumption or on idle versus work time, or engine direct hours or odometer readings, or temperatures or a host of other performance factors.
Increasingly, that kind of information is helpful, whether you’ve got a single tractor or a fleet to monitor and maintain.
“Anything electronic is going to be on this one whole network,” says Craker, who specializes in telemetry and fleet management issues. “It used to be that everything was on its own wire, so if you wanted to communicate with one electronic component on a machine… you had to have all those wires come together into a master control box that would convert everything, and it was really a lot more difficult to do. It was more of an analogue approach than a digital approach.”
- More Country Guide: Connecting the dots
What’s coming?
CAN bus has simplified that process, and a whole new window is opening. Tractors were the logical first step for CAN bus systems, and in the past five years, combines, balers and even sprayers have joined the list of important farm machinery systems where these controllers and software programs can create efficiencies. One manufacturer has even fitted its combines with an automatic controller that can make in-cab adjustments to the sieve, fan and separator settings.
Craker calls CAN bus technology an incredible opportunity that’s possible through the design of new software and controllers, and the emerging capability of sending, sharing and storing that information.
“A lot of it has to do with the terminal costs and software development which have come down to where the technology is a little more commonplace,” says Craker. “It used to be if you wanted to adjust the concave, you had to go out there, turn a wrench and manually adjust that, so there was no way for a machine to control that. But as sensors and electronic controls have come along, now we’re able to press an electric switch in the cab to move your concave up and down. And then we move to a switch to actually being on the terminal, and once it’s on the terminal, we can start writing software to monitor different sensors on the machine to automatically adjust that kind of thing.”
Next will be sprayers. Craker notes that most sprayers already have five to seven standard section controls to avoid over- or under-applying, along with variable-rate application capabilities. Those systems have been a part of RoGator and TerraGator models for several years. What’s new is that CAN bus technology can oversee those section controls.
For Craker, the take-home message isn’t as much about how advanced CAN bus technology is. It’s the connectivity and the enormous potential that it brings to the industry. He credits the Agricultural Industry Electronics Foundation (AEF), formed in 2008, as a key driver in working with the equipment industry to standardize an interface that enables different precision ag systems to communicate with one another, regardless of manufacturer.
Seven manufacturers and two equipment associations united to create this international platform, bringing together more than 150 members. The key focus of the AEF now is on ISO bus technology, which would negate the need for different monitors for different implements.
“CAN bus is the underlying technology that makes it all work on the machine,” says Craker, adding that ISO bus is the “next step” in data management technology. “It’s all the connectivity and getting the information from that machine’s bus to the Cloud and, for example, on to mobile devices, that are the new and exciting developments.”
Increased efficiency
What’s also enticing about the CAN bus systems is the increased efficiency a farmer will enjoy, and how that will free up time in the work day. Chris Carrier, marketing manager with New Holland, sees CAN bus technology opening the door on systems that are currently in development, including telematics to streamline information gathering. From his perspective, the remote troubleshooting, or being able to remotely view displays inside the equipment, is a major development.
“You can see where companies are now able to remotely access a display inside the tractor,” says Carrier, who oversees New Holland’s precision land management technologies and T7 series tractors. “Then from a support standpoint, the person at the other end of the phone is better able to help the customer with their issue, rather than the customer explaining what’s on the screen.”
Carrier also believes the processing of data will be the next big thing, including the use of the Cloud — and there are signs of that already taking shape.
“We’ll be able to build service plans around that,” Carrier explains. “Now the technician is able to see what that fault code is before he goes out to the farm, so at least he has an idea of what he’s coming out there to fix or at least he has the right parts.”
But Cloud-based sharing of data and information will also contribute to subsequent model enhancements. As technicians and dealers begin to aggregate data from a larger number of machines, they can apply that knowledge to tweak specifications and enhance the existing technologies.
“The whole strategy here is to keep everything connected,” says Carrier. “The CAN bus system already collects a tremendous amount of data in the field, and now we’re going to be able to process that data a lot faster and get it to where that’s going to be the real game changer.”
Foraging in the future
Balers have already made that next step to the ISO bus system, enabling an operator to monitor quality parameters such as moisture, with the potential to apply a preservative to reduce mould.
“It simply allows the baler to talk to the tractor and the tractor to talk to the baler,” explains Craker, again noting the potential for software development on existing technology. “We’re looking at expanding that, looking at what we could do with sensors on tillage equipment, so you could monitor depth and help keep your implement level. Hardly anybody ever goes out and levels a disc after the initial setup, but if we can get some sensors on board, we can make it easier to monitor, we can then start controlling that implement better and get better, more consistent performance.”
This article first appeared in the 2014 Soybean Guide