It was one of those great opportunities that I savour. I was with two very senior executives from one of the full-line manufacturers, and we were having a casual and candid conversation over lunch. We were in a private dining room on the grounds of the Agritechnica machinery show in Germany.
Eventually the conversation drifted to the electric-drive concept machines that were attracting so much attention at the show.
The reality, commented one of the executives, is that there really isn’t any technology on the horizon that can compete with the energy density of diesel fuel. Their view was that those alternate-energy vehicles were unlikely to progress beyond the concept stage, particularly the electric-drive machines.
Read Also
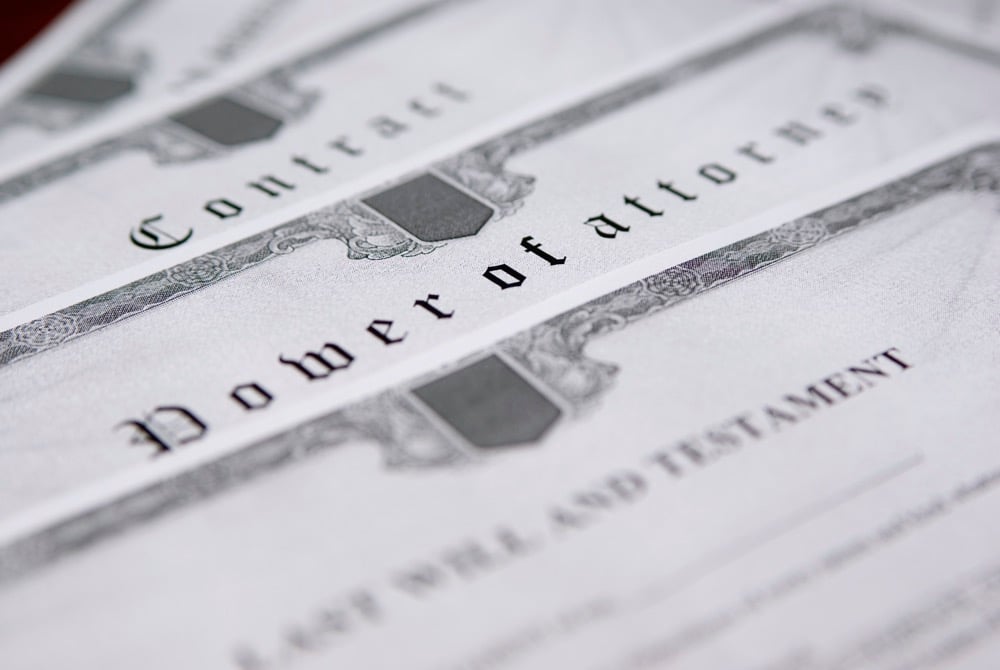
Wills and powers of attorney: the basics and why you need them
Every adult should have a will and powers of attorney. In this article, we explain the basics of these essential…
Until, of course, there are technology breakthroughs that overcome that limitation.
So I asked, “Then why bother showing them?”
There are a few reasons, the executives explained. First, there’s an element of good old-fashioned bragging. “Take a look at what we can do,” as one described it. Second, it gives engineers and marketers a chance to introduce ideas and get feedback from potential buyers. What do they think of it? Where might they want to use it, or aspects of it? It also introduces new engineering ideas to potential buyers, allowing them to get comfortable with the concepts.
It’s unlikely anyone who walked the aisles of Agritechnica this past November could come away without feeling that they had been introduced to the idea of electrification in ag machinery. It seemed clear that electric drive is one of the cutting-edge concepts that is back in vogue. AGCO’s Fendt brand displayed its e100 Vario tractor that offered four hours of run time “at average load.” It garnered the company a Silver Innovations Award from the show to hang on the wall at corporate HQ.
But the hard reality is — as those brand executives pointed out — the practical application of that machine is still pretty limited. (These executives weren’t from AGCO, and their brand had shown its own electrified tractor earlier, but it wasn’t on display at this show.)
Four years ago, Agritechnica’s aisles were home to a lot of electric-drive systems (relatively speaking), and the engineers I spoke to about them then were high on their potential. But in the last few years, that enthusiasm seemed to wane, and there was little in the way of electrification to see at the 2015 show. That lull, however, seems to be over.
Electric technology is again in the spotlight. Electric-drive innovations populated the halls this year and ranged from complete vehicles to driveline components designed to replace mechanical or hydraulic systems. But did the push toward electrifying ag equipment ever really go away?
“I kind of believe that it’s been ongoing,” says Michael Pankonin, senior director, technical and safety services, at AEM (the Association of Equipment Manufacturers), which represents most of the U.S-based manufacturers of ag and construction equipment. “When new concepts are introduced, they’re kind of the shiny objects that catch your attention, and then it somewhat normalizes. There are more and more pieces of hybrid equipment coming out.”
That’s particularly true in the construction sector, where a number of hybrid machines from a few brands have already hit the marketplace.
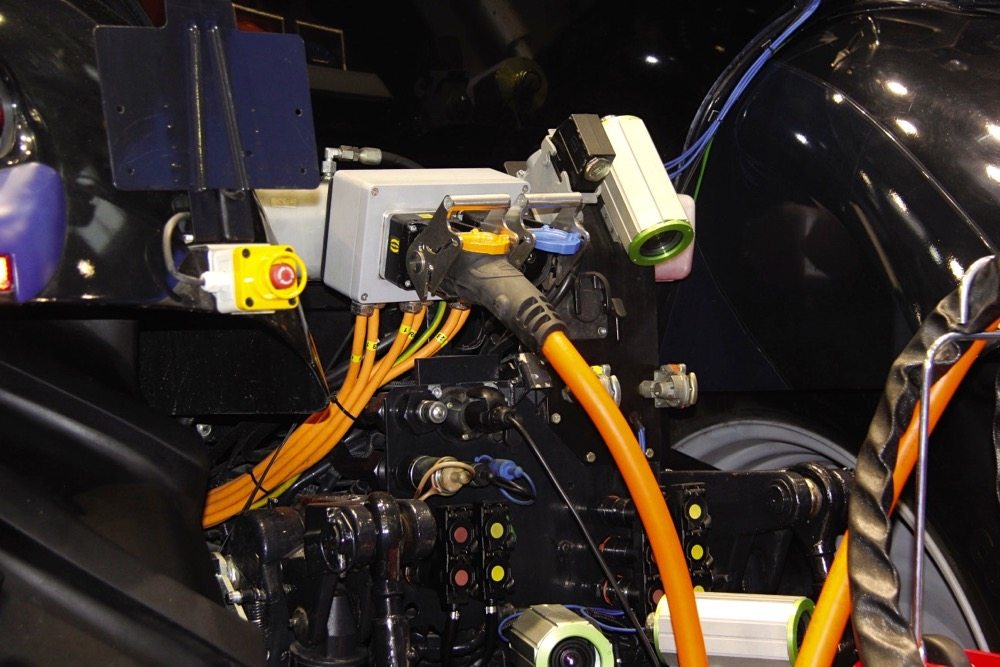
As evidence of the increasing interest in electric drives, the University of Nebraska hosted a conference on the subject the week after Agritechnica closed its doors. The Nebraska event saw engineers and representatives from industry as well as academia gather to discuss the hurdles and possibilities.
And just what conclusions were attendees left with?
“The prevailing sentiment that I heard in Lincoln was we’re probably going to move, over time, quite strongly into a hybrid-type product before we move to full power in the field through a battery,” says Pankonin. “The energy density was one of the discussions that came up quite frequently. With the amount of energy you can carry around in a tank of diesel fuel, it’s hard to beat that with a battery pack. It’s hard to even come close.”
This year that notion seemed to be the clear understanding of many of the engineering firms exhibiting electric driveline innovations in the Systems and Components display halls at Agritechnica, all of which could help move ag machines along the trend toward hybrid drives in the very near future.
“We’re hoping manufacturers will see these here and will want to work with us,” said a representative from ZF, a Germany-based transmission and driveline components company, as he stood in front of a pair of new electric front-axle drive motors for a tractor at the show.
The ability to easily vary the rotational speed that electric motors offer provides an easy way to eliminate the driveline stress that MFWD tractors experience when front and rear axles need differing rotational speeds, particularly during turns or as uneven wear develops between the front and rear tires. Electric drive motors can easily compensate for those differences as needed.
“You run that diesel in a steady state and then use the driveline to control delivery of power to the ground, tool or whatever you’re doing,” explains Pankonin. “My sense is that’s probably the direction we’re going to go.”
And there are other advantages to that kind of arrangement. At the Nebraska conference an engineer described how one new hybrid design put as much torque to the ground with a smaller engine and electric driveline than a comparable conventional design. And it offers the added advantage of reduced emissions.
“With a hybrid-type product with a diesel engine running in a steady state, you can really improve efficiency and clean up emissions,” agrees Pankonin.
Back on the grounds of Agritechnica, Markus Frey, a technical sales rep for the German electronics firm STW, spoke with Country Guide while standing beside an electric, multi-purpose concept vehicle his company had created for the show.
“We took a machine from one of our customers, switched off the diesel engine and added our electrification products and then we made a completely electric-driven vehicle,” he explained. “What we want to show is we’re the right partner for the OEMs.”
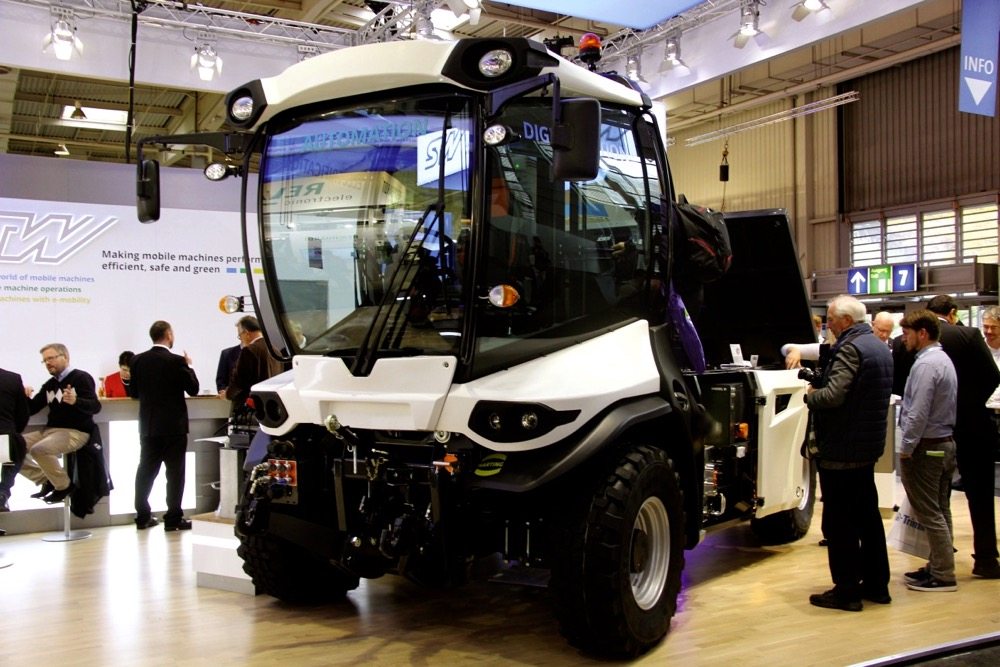
Although STW’s concept vehicle was fully electric, the company primarily wanted to show it can offer all the expertise needed to add hybrid drive or individual components to any machine. Like many of the attendees at that Nebraska conference, STW believes the best short-term market opportunities are in blending electric driveline systems into existing platforms, leaving a diesel engine up front.
“It can be a hybrid machine,” Frey says. “We keep the diesel engine, then to save energy we don’t drive with hydraulic motors, we drive with electric motors. We can also recoup energy, so for the time we don’t need the diesel engine we can run with electric energy.”
The work by AEF (the Agricultural Industry Electronics foundation) to standardize electrical implement connections has been continuing over the years as well, essentially getting ahead of widespread use of the technology to prevent, as Pankonin describes it, something like the old “Beta, VHS” incompatibility problem.
“It has certainly moved beyond the theoretical into the more practical,” he says of the evolving AEF standards. “Frankly, the thing is designed around some pretty serious power transmission. They’re looking at 700-volt direct current and up to 150 kilowatts of power. Not all tractors are going to be able to put that out, but they didn’t want the connector or the interface to be a limiting factor.”
Such a system has the possibility to take over many of the driveline functions, like a PTO, or hydraulic functions, Pankonin adds. “I think it’s recognized that that has some really significant advantages.”
Looking further down the road, as technology evolves, so does the potential for the evolution of practical, all-electric machines. But battery capacity remains the limiting factor that will need to be overcome.
“These guys at Lincoln are working on some really cutting-edge stuff,” says Pankonin. “One of the speakers said they would probably get another couple of years (of advancements) out of the lithium technology in use now. But they’re certainly looking at new battery technologies that sounded fascinating. They were talking about a solid-state battery. I have to look that up. I’m not even sure what that is!”