In times of tighter margins, most farmers step up their search for some advantage to improve their farming operation. Whether it’s new or old, they’re hoping to find something that boosts production, trims costs or, even better, does both.
Even sweeter is if that innovation was developed through the vision of another farmer.
That helps explain the success of Leading Edge Industries, a company in South Dakota created by fourth-generation farmer and entrepreneur Shawn Gengerke. In the past four-and-a-half years, he has launched two patent-pending technologies with his Load Judge and the Operation Harvest Sweep, both designed to enhance on-farm efficiency.
Read Also
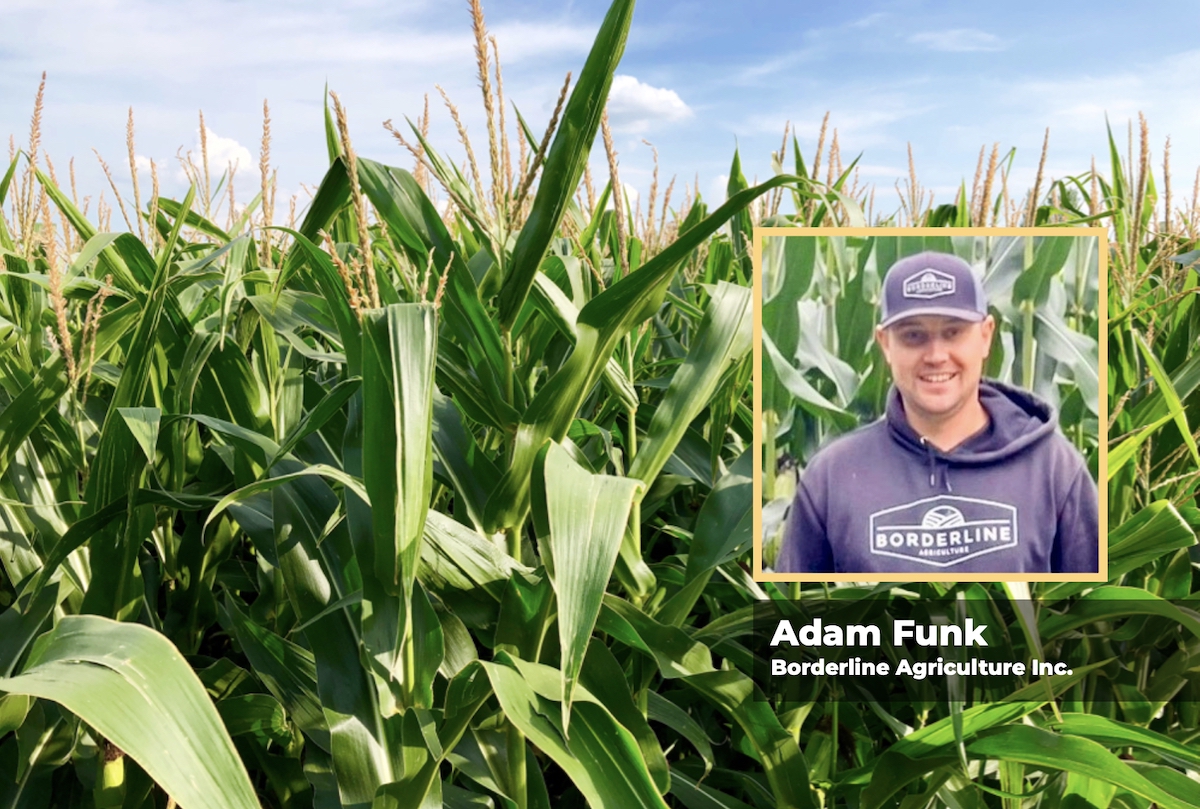
Agronomists share tips for evaluating new crop products and tech: Pt. 3
With new products, new production practices and new technology converging on the agriculture industry at a frenetic pace in recent…
The Load Judge was the first product that Gengerke brought to the market, and its sales are progressing nicely, including some limited purchases by Canadian growers.
At first glance, the Load Judge looks like a scale or moisture sensor, but Gengerke is quick to say neither is correct. The kit for the Load Judge consists of six self-calibrating light sensors and a moisture sensor, all of which are installed on the interior of the truck trailer. The computer algorithm that Gengerke helped design calculates the data from those sensors — including the physical shape and size of an incoming load — and transmits that data to a Smartphone or tablet via a wireless network that’s part of the kit.
The operator never has to leave the cab.
“Anybody can sync on, you have the data coming out on Wi-Fi, so anybody with our software can link onto it with a smart device,” says Gengerke, who farms near Groton, South Dakota. “It’s not just for the guys loading out of the bins or out of the elevator, it’s a year-round product, because once it’s in your truck, it’s always with the truck, and anybody with our app can run it.”
The sensors can be set to desired load lines, with those settings saved for future use. The Load Judge monitoring system also senses moisture levels, which is a definite advantage given the difference in piling characteristics between wet and dry commodities. That means consistency in loading, no matter the commodity: it can be grains, oilseeds, wheat, fertilizer, salt — even small rocks or stones — whatever the need.
“The Load Judge fixes a real problem because it’s the only technology that will not be defeated by dust build-up,” says Gengerke. “If you talk about logistics and equipment working correctly, there was nothing on the market that would help us, so finally we built our own.”
After three and a half years of R&D, the design has been on the market since January 2014 and has garnered three different awards — one as an AETop 50 award winner in global innovation from the American Society of Agricultural and Biological Engineers (ASABE), one from Farm Industry News and another as the favourite innovation pick for 2014 from the Farm Progress Show in Boone, Iowa.
The biggest misconception about the Load Judge is that it’s a scale, although an estimator is built into the system that Gengerke says will come to within one to three per cent of the actual weight. It also provides moisture readings for blending and directing traffic at harvest time.
According to Gengerke, the big value of Load Judge comes from real-time positioning of the grain, no matter if you’re loading fast or slow, out of bins or out of a grain cart into the truck. You can monitor it so you know when to move at the right time to make the load the same way every time. Best of all, it’s all done from the cab, so the operator is out of the dust and also out of the cold weather.
Operation Harvest Sweep

In 2012, shatter losses were even worse in corn than usual because the dry growing conditions led to faster-than-usual dry-down.
So, shortly after that harvest, Gengerke started working on a prototype for a kit that would reduce the impact of shatter loss rather than try to find a way to prevent shattering from happening in the first place. He built his prototypes and ran them for two harvests through almost every conceivable harvest condition, and he found they worked as he had hoped.
Gengerke says Operation Harvest Sweep could reduce shatter loss in corn by 80 to 85 per cent, with the potential to pay for the cost of the kit in as little as one year. He even provides the calculations on the system’s website, including savings of roughly $24,000 (assuming five-bushel-per-acre shatter loss on 1,500 acres of corn and a US$4 price for corn).
“We were losing between eight and nine bushels per acre in 2012, and that’s what started it,” says Gengerke. “The corn header hasn’t changed for 60 years; it’s still two rollers that pull the stalk down and shear the cob off. We’ve just become accustomed to accept that we’re going to have shatter loss and it’s going to fall out of the head. Yet right now, with economics the way they are, we can’t afford to lose anything.”
Combining corn over 20 per cent moisture can mean a loss of one to three bushels per acre. By the time you get down to 16 or 17 per cent, that loss increases to three to five bushels, depending on harvest conditions. And then in a stress year such as 2012, or if the crop dries down faster than normal, losses can approach eight or nine bushels per acre.
Installation can be done in as little as 15 minutes per row with each kit containing upgraded deck plates, gathering chains and impact pads. The deck plates are just one of three unique innovations — with a custom retaining lip that is unlike any OEM deck plates from the manufacturers. The second main component is the gathering chain. The Leading Edge design has a paddle that helps direct the kernels but also aids in holding the impact pad sweeps.
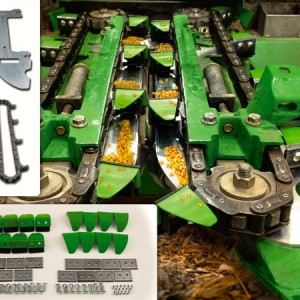
That’s important, says Gengerke, because when the shattered kernels hit the deck plates, you still have to get them up into the auger trough. The third component is the impact sweep itself, which covers the chain paddle and spreads out the impact surface, so it’s a smooth flexible surface instead of a hard metal paddle. That also reduces impact energy as the corn is harvested.
Again, Gengerke emphasizes that Operation Harvest Sweep will not stop shatter loss. Instead, it will retain shattered kernels to reduce the loss in the field — as well as any subsequent germination of volunteer corn.
That’s also becoming more of an issue in corn production regions. With newer corn hybrids that dry down faster, the volunteer corn issue is harder to control This system can reduce that issue, including the cost of herbicides, passes with the sprayer, and any yield losses in subsequent crops.
“Volunteer corn is costing us huge amounts of money — not only in chemicals to kill it but also in terms of the nutrients and water it takes,” says Gengerke. “You not only have to spend money to kill it, it also costs yield.”
Sales of Operation Harvest Sweep systems are doing very well now, with the product on the market since late January.
Additional information
There is plenty of information on these two systems from Leading Edge Industries, with videos, FAQs, return-on-investment scenarios, order forms and contact information.