Long before the foundations ever got poured, or even dreamed of, Zenneth Faye was already on the road toward Milligan Biofuels Inc., Canada’s first canola-based biodiesel fuel plant, in Foam Lake, Sask.
In fact, he traces his role in its origins to the mid-1980s, when he got involved with Saskatchewan Canola Growers Association and he was part of a group that successfully petitioned for a canola development commission that would collect a checkoff. In 1991 SaskCanola was established, supported by some 26,000 levy-paying canola producers, and Faye was on its first board of directors, chairing its market development committee.
Read Also
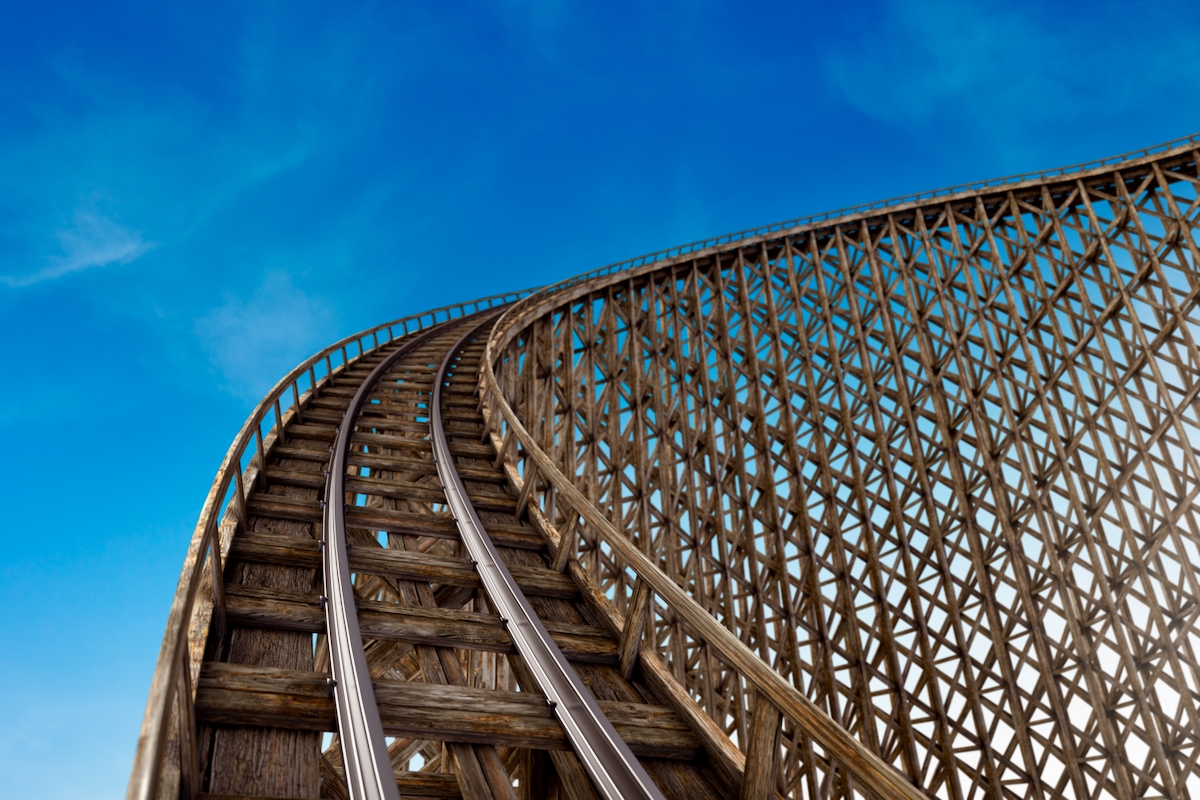
Riding the tariff rollercoaster
Farmers are accustomed to roller-coaster years. But the current geopolitical windstorm is something else entirely. On his cattle operation near…
It’s the kind of group that makes some skeptical farmers wonder whether it’s just another bureaucracy.
The board rolled up its sleeves, Faye recalls. “Through those levy dollars, we started looking at crop development and variety development,” he says. “We funded research with agronomics; we funded extension activities.”
It has always been part of his nature not to do traditional things, so it also seemed right to begin a hard look at other uses for canola too.
In 1990 while he was seeding, Faye had heard a radio report about biodiesel in Europe, where crop-based oil substitute had been mandated as fuel. The broadcast piqued his interest. Meanwhile, the Canola Commission was looking at how to make use of off-grade canola.
In a year when much of the crop froze, Faye was getting calls from all over Western Canada reporting prices as low as 25 cents per bushel. “Crushers at that time would buy it at that price and then blend it in (with high-grade canola) at very low volumes to get it out of farmers’ bins.”
The Canola Commission began some research projects with Agriculture and Agri-Food Canada. “There was a bright young grad student at that time, Martin Reaney, and we got connected with him,” says Faye. “I’m an engineer as well, and one of my old professors, Barry Hertz, was still there (at the University of Saskatchewan). The three of us were talking about opportunities one time over coffee. And we talked about how we could add some value to this very low-grade product.”
With research dollars available through the Canola Commission, they put together a small project to look at making biodiesel.
Quality and quantity
In a text book, it might look simple to make biodiesel. The reality, Faye discovered, is far more complex. When you’re using off-grade canola, the quality of the oil is never the same.
“But, at that time we were very naïve as well,” he says. “We thought we could just use some of the traditional recipes and technologies that were out there, but we quickly found that that was not the case.”
Nor is making biodiesel in the lab all that great a way to learn how to make biodiesel in larger quantities. In short, through the ’90s, the group produced and dumped lots of bad product, but a few good batches were also produced, Faye says. “When we had the good ones, we then tried to streamline the research, keep focusing on how to continually and consistently make this high-quality product.”
This was the heyday of marketing clubs in every town, and in Foam Lake the marketing club suggested they should get the word out, letting people know what biodiesel is and how it works.
From the Grainews website: Understanding biofuels
The problem was finding a place where enough biodiesel could be made. “We couldn’t get anyone in Saskatchewan to make us some,” says Faye. “We wanted about 100 gallons and we were making it by the test tube.”
They finally found a very similar product in Florida made from soybeans. They purchased some and over that summer the Foam Lake Marketing Club did trade shows around the area to demonstrate how biodiesel could be used in a vehicle. Faye had his own vehicle running on biodiesel for the summer, fall and part of the winter till the supply ran out.
By this time production in the lab had been scaled up to five-gallon-pail quantities and Barry Hertz had taken it upon himself to buy a Volkswagen diesel engine and do some testing in his lab at the university.
Adapting to the marketplace
Meanwhile, the federal government was mandating the fuel companies to decrease the amount of sulphur, a known carcinogen, in their fuels. But when they reduced sulphur, the lubricity of the fuel was also reduced, and as Hertz showed in his lab, there would also be higher engine wear.
Plus, the city of Saskatoon was looking for ways to promote itself as a more environment-friendly city. Saskatoon would be hosting an international oilseed conference, says Faye. “They wanted to have something to showcase and we said, ‘Hey, why don’t we put some biodiesel in your buses and escort these dignitaries around?’ We did that, and sort of got people understanding that biodiesel works.”
“And yeah, it works. It sort of smells like cooking, and when a bus goes by and you see that black cloud of smoke it would be like you’re cooking french fries.”
The buses were run with between five and 10 per cent biodiesel. “We were also doing some testing work on them,” Faye says. “We put posters on the sides of the buses. And we got very good publicity.”
Pitching for a place
While all this was going on, Faye was touring the province talking to various communities, trying to convince them to look at building a biodiesel facility.
In his own words, he wasn’t getting very many bites.
“Things weren’t great in Saskatchewan,” Faye says. “Economic development committees would hear about us and ask me to come and speak. We didn’t have a lot to offer except the concept. It was almost like going into the ‘Dragons’ Den’ without a good business plan and getting shot down.”
“So finally one day, I said, ‘You know if I can’t convince the community I live in to do this, it might as well just get packed up and put away.’”
With that in mind, he made one more pitch, this time to a small group of farmers and business people in Foam Lake.
And their answer was… Yes.
The town of Foam Lake
Faye felt they were finally making progress. The Regional Municipality of Foam Lake and a group of farmers threw in some cash, becoming partners on a number of projects to continue the development. “There was no technology at that time,” says Faye. “We had lots of stuff done in test tubes but nothing done to any kind of scale.”
With funds from the Foam Lake group as seed money, the group leveraged research and development grants from government, and it was this research that led to the major breakthrough.
Hertz’s work showed that their canola-based biodiesel could excel as a lubricity additive.
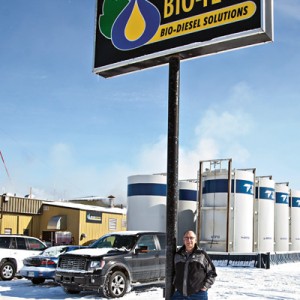
In 1996, Milligan Biotech was formed. The company went into production making a biodiesel additive that could be put into traditional diesel to increase lubricity and add to engine life. They began marketing the product in 2001.
The canola-based biodiesel and the co-products were developed by the team effort of the Bio Processing Centre in Saskatoon, University of Saskatchewan scientists and Agriculture and Agri-Food Canada. The technology is owned by AAFC, the Canola Development Commission and Milligan.
Another new product was later added after coming about by accident. Through a glitch in production of their biodiesel additive, the group ended up with a penetrating oil that was found to be much better than a certain well-known penetrating oil.
“When you plan for something and it goes the other way, you still come out with something that can make a dollar — that’s how the second product came about,” says Faye.
Because there wasn’t a small enough crusher in Saskatchewan and because their needs were not the same as the needs of a client working with No. 1 canola, they ended up creating their own crushing technology, tweaking traditional equipment to their particular needs.
Other co-products have been added. These include a rust inhibitor made from high-quality canola derivatives that is non-toxic and biodegradable, plus a road dust suppressant which can be used on clay and gravel roads, yard sites and helipads. The group also markets an environment-friendly asphalt release agent and a high-quality, high-oil meal for feeding animals.
The big news
On June 29, 2011, Canada’s environment minister, Peter Kent announced that Ottawa was moving ahead with a two per cent renewable content requirement in diesel fuel and heating oil.
When it all began with nothing more than an idea, did Zenneth Faye believe that the use of biodiesel would someday be made mandatory in Canada?
“I hoped, but I didn’t think I’d live long enough to see it,” Faye says. “The petroleum industry found that there was a good fit, but it’s not something they can make. They would have to re-tool to be able to make biodiesel. They didn’t want to do that. They offered a lot of resistance. Petroleum companies are pretty strong, but eventually it came to be.”
One of the challenges in those early days, Faye says, was that they didn’t have any production. How can you have a mandate if there is no product? That’s why in the early years Milligan needed to have a co-product, which in turn explains why the fuel additive and the other co-products were so important.
The end goal never was to replace diesel with biodiesel. That wouldn’t even be possible, says Faye. “All the vegetable oil in the world would only replace three percent of the fuel. So it’s never going to happen.”
The goal was to establish a market for off-grade canola. Today, Milligan buys over 60,000 tonnes of green, frozen or otherwise unwanted canola seed per year, produces over 20 million litres of biodiesel from their facility in Foam Lake that employs 46 people.
Milligan Bio-Tech Inc. is now Milligan Biofuels Inc. and its first executive manager, Zenneth Faye, no longer works at the plant but he’s still with the company in an advisory capacity. And, he’s still fascinated with the idea of finding more uses for damaged canola seed.
One of them is glycerine. Depending on purity, there are a number of products in which it can be used. Pharmaceutical glycerine is the top end. At the present time, glycerine from Milligan is being sold for processing elsewhere, but…
“It’s like when you make doughnuts, you have the centre of the doughnut left,” Faye says. “You make Timbits and get more than you would for the doughnut. The leftovers have value too. They just need a little processing and development work.
“That’s the part I like. You asked why would I leave when everything was going so well. With my — what I was given by God or whatever — that’s the part that intrigues me. I love dealing with the unknown. That’s probably why I’m still farming.”