The 2016 growing season saw the advent of a new technology — Roundup Ready 2 Xtend soybeans, along with its herbicide companion, XtendiMax. The technology had been anticipated for more than five years, particularly by growers in the southern U.S. where resistant weed species and continual use of Roundup Ready soybeans and cotton have been disastrous.
Although the seed and chemistry were both registered in Ontario in 2016, the U.S. faced an unexpected challenge. Dicamba-resistant soybean and cotton seed were on the market, but XtendiMax wasn’t. But many growers decided they couldn’t wait another year, so they went ahead and planted the resistant seed, and then tried to come up with their own off-label spray mixtures that they hoped would perform more or less the same as XtendiMax.
Read Also
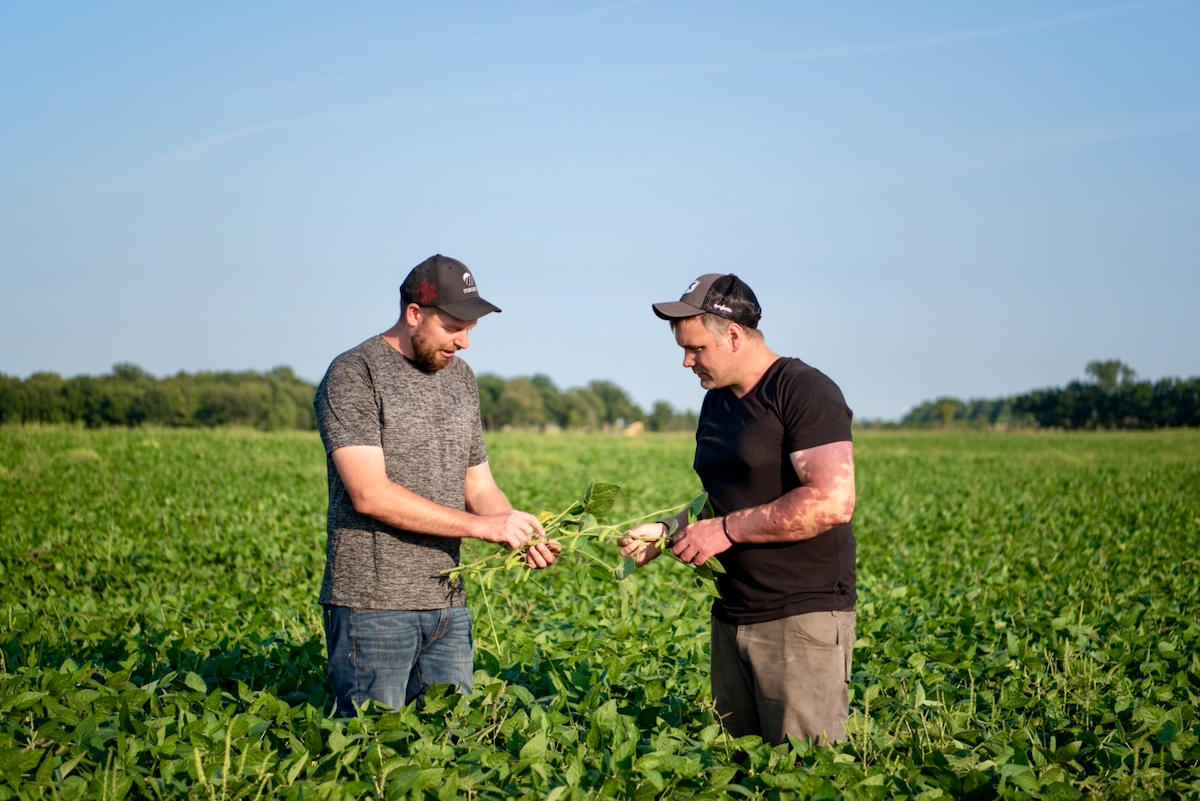
Ontario farmers partner for success
Ontario business partners, Matt Bergman and DJ Wassenaar, have been farming together for 10 years. Their focus on integrating unconventional…
In the resulting mess, there were hundreds of cases of off-target dicamba injury, in part because the dicambas on the market aren’t the same dicamba that’s in Xtendimax, and partly because the some of the sprays were applied poorly in the first place.
For Dr. Jason Deveau, it’s added incentive to make education a big focus heading into 2017. As the application technology specialist for the Ontario Ministry of Agriculture, Food and Rural Affairs (OMAFRA), he believes that the factors contributing to off-target movement remain largely misunderstood.
And with Xtend soybeans now available across Eastern Canada, the challenge is even more pressing.
- Read more: Final words on dicamba
Beginning in 2015, Monsanto went to great lengths to explain the details on XtendiMax. Sprayer settings and environmental conditions took the forefront at demonstrations throughout Ontario, with the company emphasizing ground speeds, wind speeds, boom heights, nozzle types, water volumes and application pressures, plus a triple-rinse protocol to reduce crop injury from residue carryover.
If this sounds like repetition, it is, and it’s the world that Deveau lives in. Deveau says he feels as though he’s given “the talk” on dicamba stewardship and sprayer settings countless times.
But the need for applicators to understand these topics, as well as complicated concepts surrounding thermal inversions, is perhaps more critical today than it ever has been. One need only look to the U.S. in 2016 as a warning.
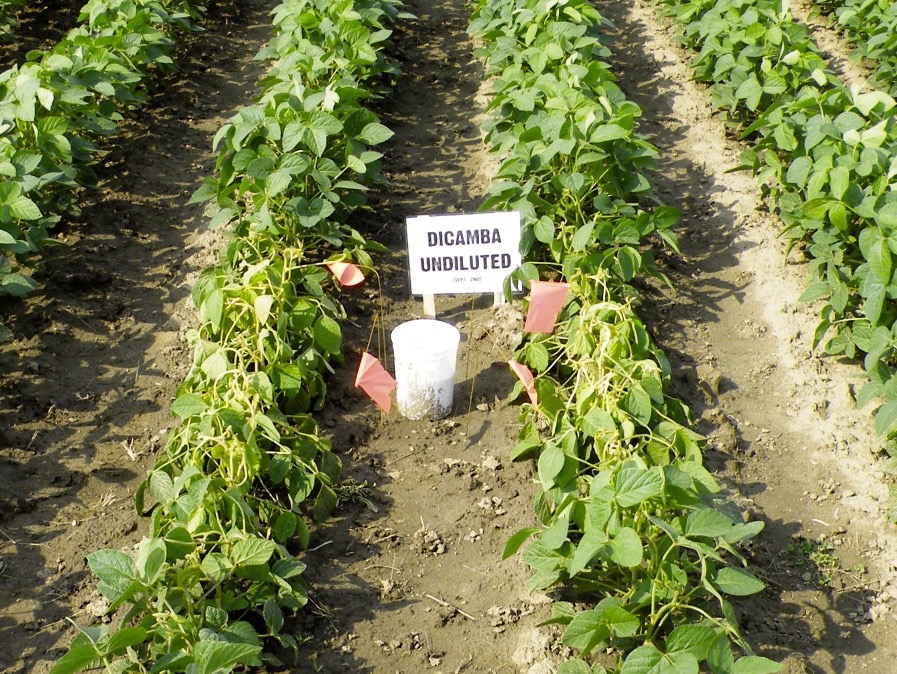
The products
It’s important to know there are differences between XtendiMax and Engenia, aside from the one being manufactured by Monsanto and the latter by BASF. Both are variations on the original dicamba product, first registered in 1967 under the name Banvel.
The original herbicide was a dimethylalamine (DMA) salt, but in 1983, in an effort to reduce its volatility, it was upgraded to diglycoalamine (DGA) and was marketed as Banvell II (or Clarity).
XtendiMax is the DGA salt with an added formulation known as Vaporgrip, which Monsanto says encapsulates the herbicide molecule to further reduce volatility.
Engenia, by contrast, is a new chemistry. BASF revised dicamba as a BAPMA salt, and for all intents and purposes, it can be considered Banvel III.
Both companies say their products greatly reduce volatility, but according to Deveau, there has been little if any third-party data to support the claims. Yet he also says that although volatility should not be dismissed, it isn’t likely as big a factor in off-target movement as physical drift and sprayer contamination between fields.
That’s an essential point, since growers may believe the new products mean applicators won’t really have to worry about off-target movement.
Deveau adds that on the whole, many of today’s applicators are more familiar with glyphosate, and may not appreciate just how unforgiving dicamba can be when it comes to crop injury, even though in Eastern Canada more growers will be applying more dicamba on more acres near more sensitive crops than ever before.
Taken collectively, Deveau says, this adds up to one very large unknown. There has never been anything like this in agrochemical development.
“We’re about to embark on the largest global experiment we’ve had in a long time in agriculture,” says Deveau.
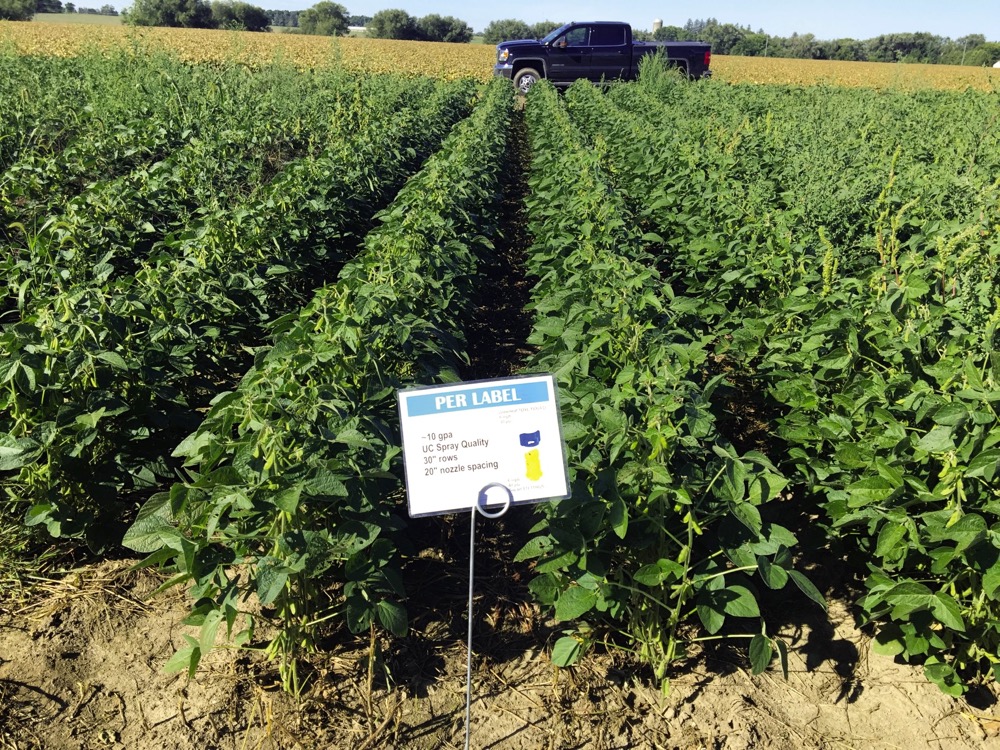
Thermal what?
The concept of thermal inversions complicates this even more. It’s similar to telling people that oxygen isn’t flammable, it just supports combustion. Thermal inversion can be just as difficult to understand.
“When the air stratifies, where you get that calm, still layer, it doesn’t matter if it’s a volatile or a very small particle, both are buoyant,” says Deveau. “Volatile or not, if you spray using droplets that are too small, or from a boom that is too high into conditions that allow it to hang there, the potential for off-target movement goes way up. When the inversion layer begins to dissipate or when that slab of air above the crop moves downhill or is pushed by a light wind, all of that suspended pesticide moves with it.”
Deveau acknowledges that growers are pressed for time, but there are some key adjustments that need to be made.
“Slowing down, in and of itself, will reduce drift because fast ground speeds cause spray to get drawn into the wake of the sprayer, and that increases drift potential,” says Deveau.
Another measure that helps is to drop the boom height, which is also easier if you slow down. Slowing down reduces sway, Deveau points out, and this allows the operator to lower the boom.
It’s also important to keep in mind that with everyone watching so closely, there are bound to be cases of suspected vapour drift. However, dicamba injury can be tricky to diagnose, and symptoms from physical drift can show up long after the assumed window of opportunity for such a phenomenon.
Plants need to be actively growing for dicamba injury to make itself known, Deveau explains.
However, it’s worth noting that dicamba has been used in corn for several decades. Deveau recalls that it was Dr. Peter Sikkema, from the University of Guelph’s Ridgetown Campus, who pointed out that it’s been used with little or no difficulty. If there was a concern, it was with sprayer carryover and physical drift.
Last but never least
Deveau and Monsanto are insisting on effective sprayer cleanout.
The protocol consists of seven steps:
- After spraying, drain the sprayer (immediately).
- Flush the tank, hoses, booms and nozzles using clean water.
- Prepare a cleaning solution with an ammonia-based commercial cleaner.
- Remove and soak all strainers, screens and filters in solution (preferably overnight).
- Fill the tank with cleaning solution, agitate and thoroughly recirculate for at least 15 minutes. Remove all visible deposits from the spraying system.
- Flush hoses, spray lines and nozzles with cleaning solution for at least one minute.
- Repeat steps 1 and 2 an additional time.
It’s also important that farmers appropriately dispose of all rinsate in compliance with applicable laws and regulations. Growers must pay particular attention to addressing so-called “dead-ends” in the sprayer. Growers who haven’t rinsed the inductor bowl, or filters or emptied their section ends (or installed air-aspirating end-caps) may be in for a rude awakening.
“I talk about Europe’s adoption of the ‘continuous rinse method,’ and I think there’s a place for that here,” says Deveau. “We’re still exploring how tank-cleaning additives like ammonia and the dead-end plumbing issues come into it. Dilution is the key to effective cleaning, so the grower still has to get out of the cab and deal with any plumbing that the rinse water couldn’t get to.”