More centrifugal force with New Holland
The New Holland CR9000 series combines rely on the New Holland s exclusive Twin Rotor design for threshing and separation efficiency. On the largest CR9000 combines, the twin rotors are 2,638 mm long with a diameter of 559 mm. According to New Holland, these twin rotors generate 36 to 40 per cent more centrifugal force than any other rotor design, moving the grain swiftly for faster separation and threshing.
New Holland emphasizes that their Twin Rotor technology causes less grain damage than competing hybrid threshing and separation systems partly because there is no combination of transversal and longitudinal drums or rotors that can create crackage.
Read Also
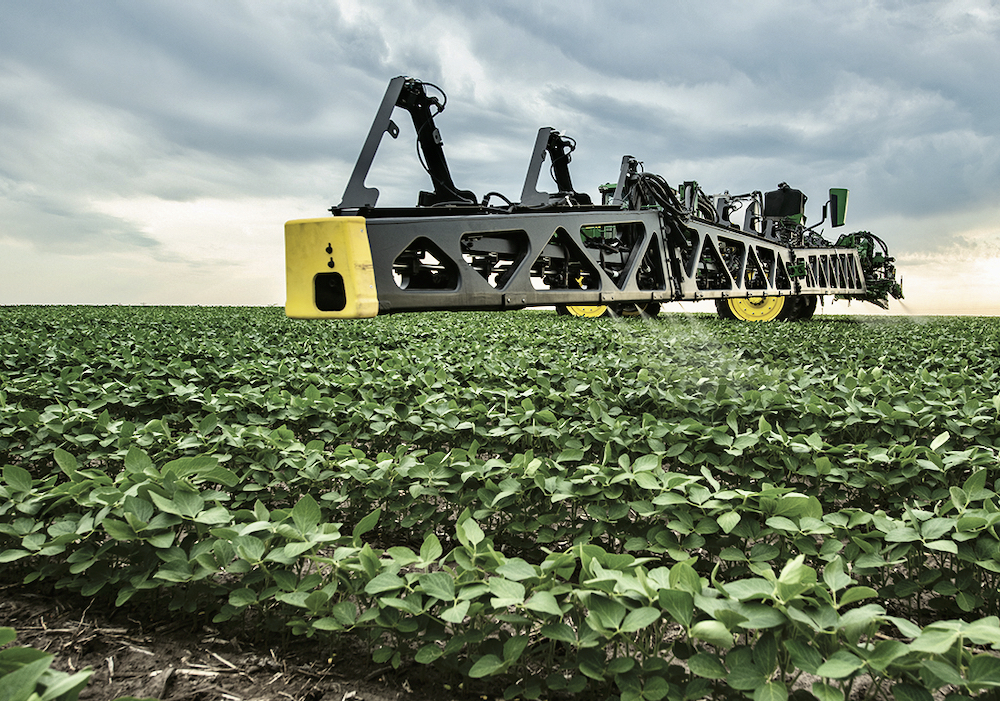
Farm machinery scores big in 2022
When I spent a summer working as a mechanic’s helper at an Allis Chalmers dealership in 1978 as one of…
New Holland s CX 8000 super conventional combines use the more traditional cylinder separation. The 29.5-inch diameter threshing drum is the largest in the industry. There are ten rasp bars on the drum driving the crop into the concaves. The cylinder acts as a flywheel creating high inertia to even out crop loads. The CX 8000 concave surface area is large, and with a concave wrap angle of 111 degrees, it creates 1.18 sq. metres of threshing area.
Rifling grooves drive JD s bullet rotor output
John Deere s 70 series STS combines rely on their Bullet Rotor for threshing and separation. According to the company, Bullet Rotor technology reduces the force required to move material through the combine by as much as 20 per cent. The technology is also said to produce better throughput in green, ropy crops, and to deliver more efficient separation in all crops.
John Deere says that the rifling grooves on the elements allow the bullet-shaped rotor to move large volumes of crop material through the rotor more efficiently. Heavy-duty vanes (which the company says never need adjusting) on the top cover of the STS module help propel the crop rearward and through the threshing and separating system.
The John Deere STS module features a stair-step design that gives the crop mat room to expand as it travels through the separator module. This reduces the chances for roping and lowers power requirements. An extended-wear separating package is available. It doubles the life of the components and includes factory-installed extended-wear concaves, threshing elements and separator tines, and rotor-top covers.
Starting with Case IH transition cone
The Case IH Axial-Flow threshing and separation system consists of a rotor transition cone, a rotor cage and concave module wrap around the AFX rotor. The company says the patented transition cone with impeller system on the front of the axial flow AFX rotor smoothly accelerates the crop mat, promoting positive material flow with less impact and superior threshing and separating performance.
A single-line axial flow rotor surrounded by a concentric rotor cage facilitates gentle, multiple-pass grain-on-grain threshing. Exclusive adjustable rotor-cage vanes allow the operator to customize crop flow to conditions for maximum performance and productivity. These vanes have three positions: fast, mid, and slow. Concave module wraps that increase threshing efficiency enhance overall capacity.
The 5088, 6088 and 7088 Axial Flow combines feature a one-piece 156-degree concave wrap, while the 7120, 8120 and 9120 come with a two-piece 180-degree concave module wrap. These concave module wraps provide for longer, more efficient threshing in the separating space, thereby boosting optimum threshing and separating capacity. Several types of concave modules that can be electrically controlled from the cab are available for different crops and crop conditions.