Earlier this fall, it was announced that Bob Dylan won the Nobel Prize for Literature. I have to admit, I didn’t see that coming. Not to take anything away from his talent, it’s just that I wouldn’t have expected to hear he had won that kind of award, any more than I would have expected to hear Rosie O’Donnell come up as a topic in a U.S. presidential election debate.
But as I walked the grounds of the U.S. Farm Progress Show in Boone, Iowa, in August and looked at the newest equipment on display, a line from one of Dylan’s songs did pop into my head. And it was the design of those new machines that made me think of it.
Read Also
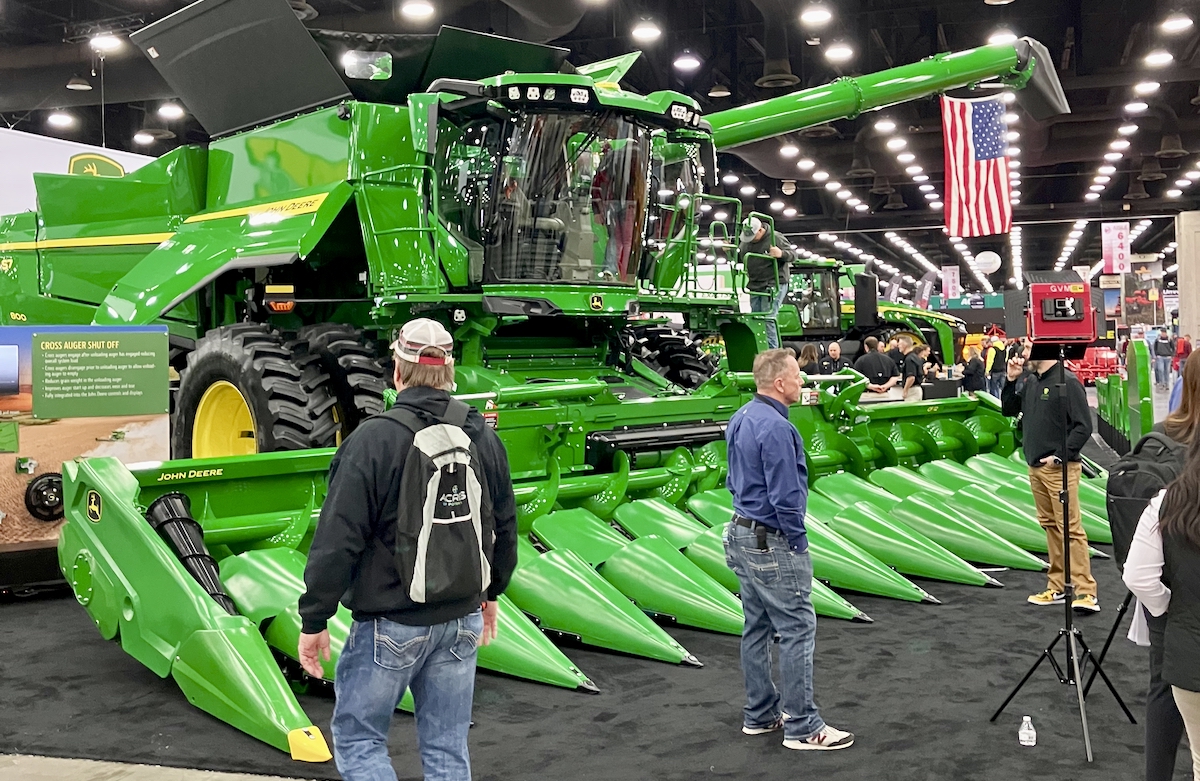
The pros and cons of new technologies
New farm technology hitting the marketplace can be awfully enticing, and it’s not been unheard of in years gone by…
What was that line? This one: “The times, they are a changin.’”
Those words from 1964 seem as valid today as they did back then. It’s just that now I see those changes reflected more strongly than ever in the evolution of farm equipment.
Over the past decade, we’ve witnessed an avalanche, with model updates in most machine categories from all brands, although digital capabilities really dominated the evolution in machinery — if you ignore the breakneck pace at which engineers worked to get diesels to meet Tier 4 Final engine emissions regulations. Even if you don’t ignore it, it was the way the brands packaged their advanced technology with the new higher-priced engines that helped make farmers feel they were getting some benefit from the growing purchase cost of their machinery.
Beyond doubt, digital technology is still a main driver of machine evolution. And it was impossible not to notice this on the grounds of the Boone show. When you pause to think that we’ve reached CNH’s driverless Magnum and T8 tractors after the early days of GPS auto-steer barely a decade ago, the scope of change becomes clear.
In the last issue of Country Guide, we provided fairly extensive coverage of those robotic tractors, and they really did dominate the landscape at the show. It’s hard to overstate the profound impact they are going to have on future equipment design — and the makeup of the whole industry. But walking past them and looking closely at what else was on display made it clear that digital evolution isn’t happening in isolation. There are also other changes moving machine design far beyond where it has been.
For example, tucked in a corner of New Holland’s display was its concept multi-fuel tractor.
“What we have here is a New Holland T6 tractor that’s been adapted,” explained Michael Cornman, NH’s livestock market segment leader. “We call it our alternative fuels tractor because it can be powered by propane, methane, bio-propane or bio-methane. What that means to a producer is a savings of 20 to 40 per cent in total costs while reducing pollutants by 80 per cent from diesel power.”
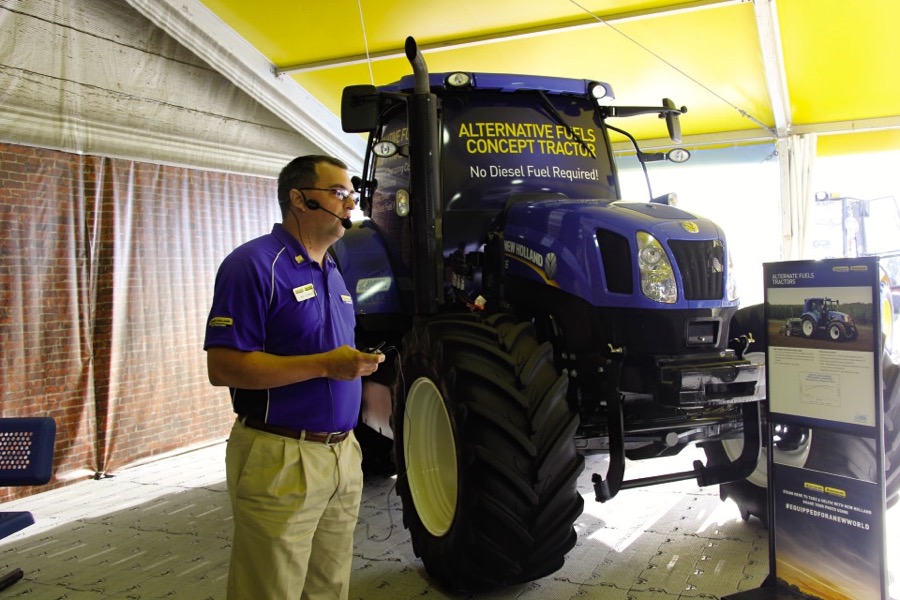
Rigging tractors to run on unconventional fuels isn’t really new for New Holland. They displayed a hydrogen-powered concept tractor several years ago. In fact, their corporate demonstration farm in Italy is set up to be entirely self-sufficient when it comes to energy, producing the biofuel it burns in machines and in the generators that produce its electricity.
“We’ve used this tractor in a series of tests and found it to perform very similar (to diesels) in terms of overall power and torque curves,” Cornman adds.
Although the cost of infrastructure required to produce biofuels to the standard required by engines is still prohibitive for most Canadian producers, the NH notion of energy self-sufficiency isn’t pie-in-the-sky anymore. Walk through many large-scale European farmyards, especially in Germany, and you will see biodigesters already working away making biofuel, mostly to power generators feeding electricity back to the national grid.
That really shakes up the traditional definition of farm-gate produce.
“We’re providing this (T6) as a concept tractor to introduce it to the marketplace,” says Cornman. “There’s more to come on this in terms of when it goes into future production, but we see a true opportunity.”
There are new materials being incorporated into mainstream equipment design, too. At its new product launch in Iowa this year, John Deere pulled the invisibility cloak off one of its sprayers that was outfitted with a boom made from carbon fibre, a material found on Formula One race cars.
Incorporating carbon fibre isn’t just to amp up the cool factor. There are good reasons to use it, despite its higher cost compared to steel or aluminum. “Its strength-to-weight ratio is much higher than aluminum,” said a Deere product rep during its official introduction to media members. “What that does for us is allow us to make a 120-foot boom that’s 30 per cent lighter. It also gives us the ability to extend to much wider widths without increasing the weight on the sprayer.”
Carbon fibre is also much more resistant to chemical corrosion that metal. And with a simple repair kit, farmers could repair boom damage in the field and be ready to go again in just a couple of hours. There’s no need for special welding skills, as with aluminum.
Besides, carbon fibre booms have already been in production on Deere sprayers sold in South America for about three years now. They’ll be showing up here within at least the next couple of model years, according to the brand.
Then there was a shakeup to the conventional notion of the combine. Introduction of the production-ready Tribine has the industry wondering if the conventional combine configuration is soon to be a thing of the past.
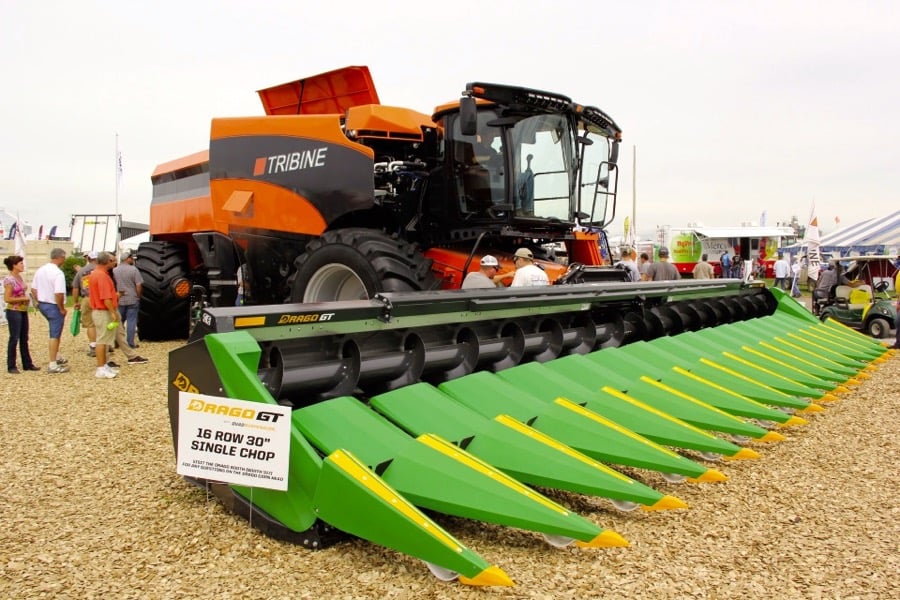
“Really, if you look at the (combine) industry, it hasn’t changed much since the Second World War,” said Tribine’s vice-president of sales and marketing Greg Terjesen as we sat talking a few feet away from the first production model, which is a merging of a high-capacity combine with a grain cart.
The concept was first shown to the public at the Ag Connect Expo in Kansas City, Missouri, in 2013. Back then, their prototype number four was based on a conventional Gleaner combine modified to work with the rear grain tank. When Country Guide interviewed company owner Ben Dillion at that time, he said he hoped to interest one of the major brands in the concept and license them to produce it.
That didn’t happen. Now a new “clean sheet” design has emerged from Dillon’s own company as it ramps up to begin commercial production of the Tribine on its own. The current machine incorporates the firm’s newly developed threshing body design, using one of the largest rotors in the industry.
“We have the biggest threshing and cleaning system of anybody, and we have the tightest turning radius of anybody here,” said Terjesen. (Although, I didn’t see any hard stats to confirm that.)
Like all these new technologies, the idea behind the Tribine is to improve efficiency and advance agronomic practices.
“We were not only looking for more capacity, we were looking for less compaction,” Terjesen continued. “One of the reasons the machine is designed the way it is is to lessen compaction. Here you have a machine that weighs 42,000 pounds, but it only makes two tracks. Add a tractor and grain cart to that and all you’re doing is compacting the soil.”
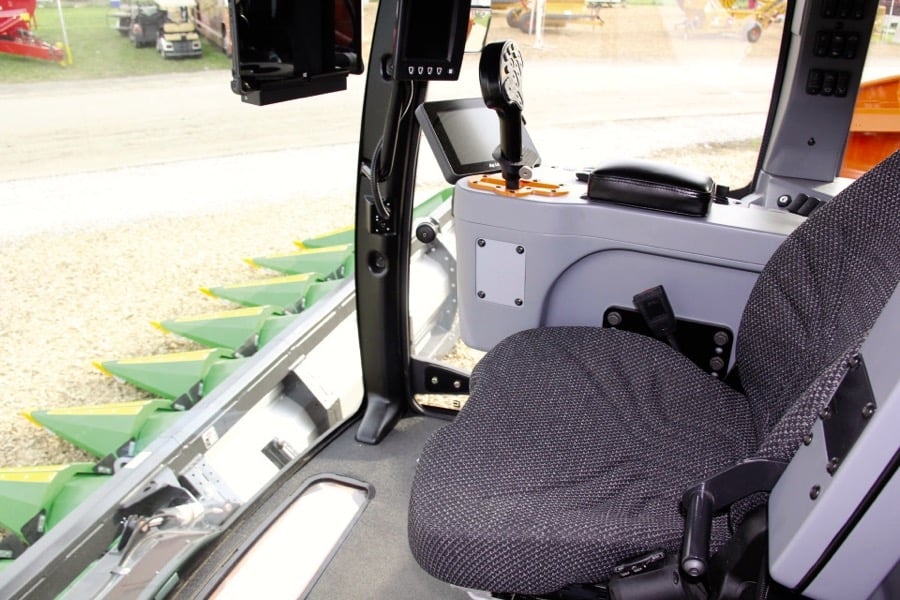
Since the public introduction of prototype number four back in Kansas City, new technologies have emerged that help the production Tribine limit the affects of compaction.
“During that three-year span, the floatation tires you see here came out,” said Terjesen.
And engineers didn’t just restrict their attention to the big picture of blending a combine with a grain cart. Inside the cab, they provided operators with a very different environment than what’s offered on models from the major brands.
“The other thing we’ve done is eliminated the steering wheel,” Terjesen added. “We’ve gone with a single joystick control. The farmer is always looking forward and to the sides, because that’s where the header is. By getting rid of the steering wheel, we could put a glass bottom in the cab, so they can look down and see exactly what’s going on.”
The joystick steering concept has already appeared on equipment in the construction sector.
“We’ve had that machine out testing with farmers, listening to customers, trying to get their input on what we should do better to leapfrog the competition, which is what is really our goal,” said Terjesen. “We say the future of harvesting is now.”
It might be fair to say the future of all ag equipment is now.
Because, as Dylan said, the times, they are a changin’.