David Normandin and his brother Mathieu preferred driving tractors to milking cows and that’s why they make hay and not milk.
The brothers, along with their father Luc and Luc’s partner’s daughter, Audrey Mailloux, operate Norfoin Inc., 57 km southeast of Montreal in the Montérégie region of la belle province.
The operation had been a dairy farm started by David Normandin’s grandfather in 1958, but switched to haymaking in 2000, Normandin told a tour group attending the Canadian Forage and Grassland Association annual meeting in nearby Bromont on November 17.
Read Also
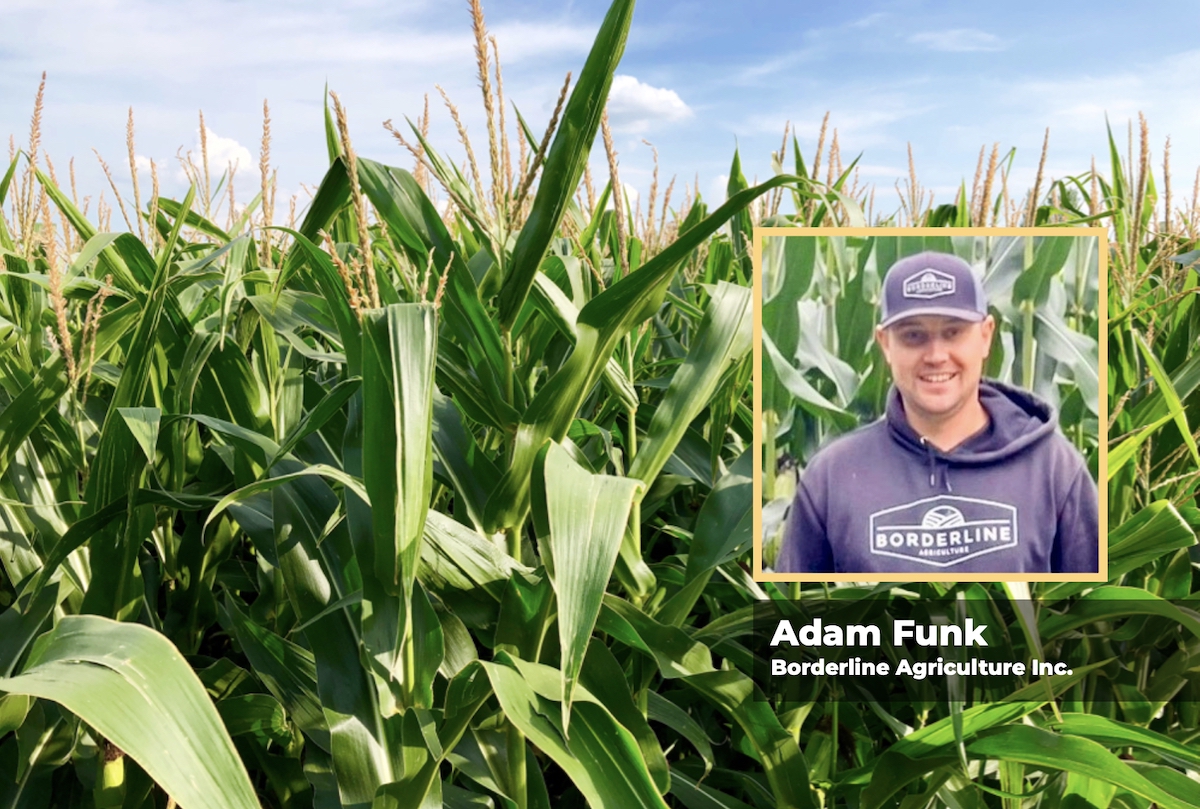
Agronomists share tips for evaluating new crop products and tech: Pt. 3
With new products, new production practices and new technology converging on the agriculture industry at a frenetic pace in recent…
The company also provides snow removal services during the winter.
The family operation puts up around 6,000 large square bales from its own 618 acres of land, plus bales from another 198 acres under contract. It also buys 6,000 large square hay bales.
The Normandins dry almost all their hay, have almost an acre of inside hay storage, including a new 50×110-foot building, which will eventually be heated, and they can convert large bales to small square ones as required.
About half of Norfoin’s hay is sold in Quebec and the rest is exported to the United States through hay brokers, Normandin said.
The company puts up various hay mixes, including alfalfa, timothy, orchard grass, fescue and clover. And the hay goes to a wide variety of livestock, including milk cows, dry cows, calves, horses and even zoo animals.
Hay buyers demand top quality so the Normandins strive to get their hay up in good condition and keep it that way.
After the hay is crimped and cut, it’s ‘tedded’ or fluffed up to speed drying. Then it’s raked and baled. The bales are picked up the same day to prevent sucking up moisture from the field. They can pick up bales as quickly as they are made, Normandin said.
The hay is baled at about 25 per cent moisture.
“We dry about 90 per cent of our hay (to 10 to 12 per cent) with a custom-made bale hay dryer,” Normandin said.
“We saw a dryer in Europe but it was really expensive so we thought about building it. We began the first year with some prototypes, then we built a dryer to meet our needs. Now we dry 100 (big square) bales at a time.”
The dryer is wood fired. Wood is plentiful and cheaper than other forms of energy, he said.
Hay and fire don’t mix. A wood fire heats water, which feeds a radiator used to warm air blown through the bales. It takes six to 15 hours to dry a bale depending on its moisture content. They can dry about 300 bales a day.
The dried bales are stacked 11 high in sheds.
All of Norfoin’s hay is put up in large square bales because it’s faster, Normandin said.
“We can do the work of 10 people with a small square baler with only four people with one big square baler,” he said.
However, five years ago, after sales of large squares slowed, the company built its own system to turn large square bales into small ones. Now half of Norfoin’s hay is sold as small squares.
The family brought a small square baler into one of its sheds, powered it with an electric motor and modified it so it turns a big bale into small ones.
Normandin said they cut their hayfields two to four times a season. Nitrogen is applied after each cut and manure is spread every spring.
This article was originally published in the 2015 Forage & Grassland Guide