For Dave Gillespie, the question of whether to install a new on-farm storage bin and drying unit was never really in doubt. At least, it was never really in doubt after the fall of 2010.
“The biggest factor was when we sat and couldn’t pick any corn because we were still sitting on beans, and nobody would take them for over a week,” recalls Gillespie, who farms about 1,000 acres on Highway 21 between Ridgetown and Thamesville, Ont.
It’s a move that points to both the opportunity that comes with an on-farm drying and storage system, and also to the way that it impacts all parts of the operation.
Read Also
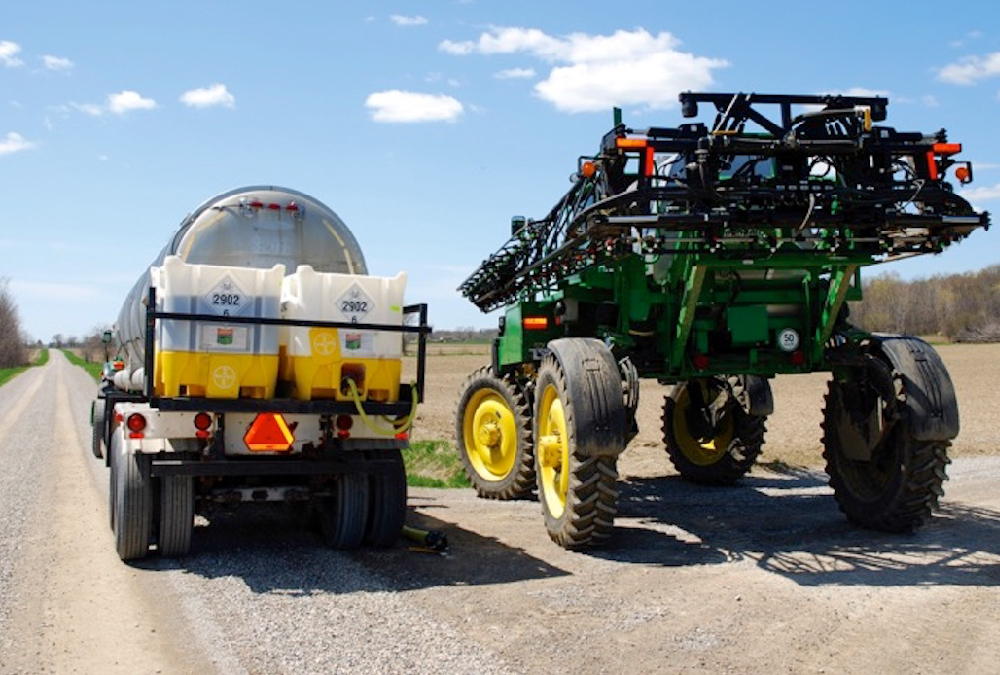
Tips and strategies for pre- and post-harvest weed control
Glacier FarmMedia – Sometimes the simplest solutions are the best ones. Breanne Tidemann, an Alberta-based researcher with Agriculture and Agri-Food…
It’s also a move that puts Gillespie in the middle of a major eastern Canadian trend.
More growers are pulling the trigger, either building new storage and drying units on their farm, or replacing existing systems or expanding them. In Gillespie’s case, it was a major upgrade. He decided to replace his father’s aging system, and he reasoned that the family farm was also outgrowing the existing system’s capacity.
Bin and dryer manufacturers have been working flat out for the last four years, with more and more farmers wanting the flexibility and profitability that they associate with on-farm grain handling.
In many cases, they see it as a version of the own-your-own-equipment versus hiring custom operators continuum. Owning your own ensures you get the work done when you want it done, and that you get it done the way you want it done too. Going custom, however, means your capital isn’t all tied up in steel.
“That’s basically what it is,” says Gillespie, agreeing with the comparison. “If you’re going to the elevator, it’s the same as hiring a custom sprayer or a customer harvester. It’s all about what your goal is, and what you want to do.”
Of course, management of time is a huge consideration too. Do you hire an expert, or do you take the time to become an expert yourself?
But then, the time discussion has two sides. If you aren’t drying and storing your grain on farm, you can be spending a lot of your harvest lining up trucking and delivery, negotiating drying rates, and waiting in someone else’s line.
For Gillespie, the decision to build his own storage and drying unit came down to logistics and marketing. There was the challenge of getting the grain harvested and stored in his previous system measured against the freedom of marketing and holding on to the grain himself.
“I wanted more capacity, because I couldn’t handle having to ship a third of our crop in the fall — and,” says Gillespie, “there were the logistics of getting it out, and I wanted to be able to sell it throughout the year, and I wanted to be able to capture the drying costs on the corn.”
“If there’s a substantial amount of grain and you’re spending a lot of time that you should be harvesting just trying to get rid of it, or if you’re paying commercial drying rates,” Gillespie says, “that’s when you should (install a new system).”
For Gillespie, there is no reason why farmers shouldn’t have some storage on their farms. In fact, he goes so far as to suggest that there should be storage capacity for at least half to three-quarters of the crop on any farm. Unless a farmer lives next door to an elevator and can unload easily without significant wait times, he believes, then the move towards larger farming units that are often spread farther apart necessitates on-farm storage and drying systems.
Helmut Spieser, engineer with the Ontario Agriculture Ministry also sees more farmers building new on-farm systems, and for the most part, he believes it’s a sign of some shrewd thinking.
With larger farms, as well as with today’s bigger yields, most farms are dealing with steadily increasing grain and oilseed volumes. Besides, timelines are getting tighter too, and there’s less margin for inefficiency.
Plus, more growers are building their new units in the hopes of becoming inland satellite locations for some of the larger commercial elevators, so there may be even more income opportunities.
But it’s not as simple as it all may seem.
“If they have the assumption that ‘just because I put a system, I’m going to make a whack of money,’ they’re going to be disappointed,” says Spieser.
In effect, with larger farms, higher yields and rising land prices, there is simply too much at stake to leave anything to chance, and Spieser points to wheat to explain why.
Quality is paramount, and with wheat’s current pricing structure and with its sprouting potential and its specific quality uses within the food industry, the stakes get very high very fast. It’s a trend that helps explain Spieser’s belief that if you have a large on-farm system, you should have one person dedicated to managing that system. It shouldn’t be a part-time responsibility, or something that you think you can squeeze into a few in-between moments scattered through the day.
“Somebody has to look at it, aerate it, turn grain, move grain, ship it out, or whatever needs doing,” says Spieser. “That needs a full-time person who’s responsible for that. You have to have some continuity and capability there.”
Turning and aerating is important, but again, with wheat even more than with corn or soybeans, in part because it’s stored through so much warm, muggy weather.
As well, insect pests are another learning curve and can be a bigger threat in wheat. Since wheat is harvested at the height of summer, it’s also the height of insect activity, and as Spieser notes, it’s the first “fresh food” in the bin.
“Again, you have to manage it, because the tolerance in the industry is zero,” says Spieser. “That’s zero for live insects at the receiving plant and in some cases, they also want zero dead insects, because if they find dead ones, they say, ‘There’s an off chance there might be a live one in the batch.’ If they find them, they’ll send you home.”
Corn can provide a similar challenge with bugs but typically only in those cases where it’s stored for more than a year.
The good news is that there are many different resources available to growers looking for information on storage bins and drying units, Spieser says. In particular, Ontario’s Ag Ministry hosts workshops on storage and drying, and also offers written articles and does presentations at Ontario Soil and Crop Improvement Association meetings. Some dealers will help a grower with the initial operating instructions and perhaps some rudimentary training. However, some of the technical detail beyond how the auger works or how the dryer works can be left out, sometimes with very unfortunate results.
“I say that I dry a lot of grain on the phone,” Spieser says with a chuckle. “I can usually sense the guys who have the system for the first year because I talk to them about three times through the growing season. ‘This is how it went in, it looks like this, it smells like this.’ ‘Trust me,’ I say, ‘it’s fine. Run the fan.’ But they need to know what they need to know, and unfortunately, some don’t.”
It’s one thing to say, “This farmer says he pays 19 cents shipping whereas the mill is charging 51 cents.” But Spieser contends that these comparisons aren’t apples to apples. The price the farmer may be quoting could be for fuel alone. The price the mill quotes usually includes everything, including overhead, insurance, profit, amortization, repairs, demurrage and equipment breakdown. The two prices are not considering the same parameters.
Dave Gillespie agrees that such risks and concerns are valid, and must be addressed. But he also maintains storing his own grain is an advantage. He performs all of the necessary checks and monitoring that is needed, although he acknowledges that those processes are often more complicated than they might appear.
“You don’t just think you’re going to put grain in it, and that it’s just going to be there when you need it,” Gillespie says, echoing Spieser’s warnings. “You have to check it and manage it, and really, the only way to be checking it is to be pulling loads out through the year and moving it around.”
Like tile drainage?
As farms keep growing, and as risk management becomes more crucial, on-farm storing and drying of grains is also taking on a new value. And in many ways, hiring a professional for storage and drying is mirroring what is happening within the tile drainage sector — where some farmers have to wait up to two years to get a crew on the farm.
These are what Spieser calls “the typical expansions,” where farmers add a bin, which is usually larger and taller than any existing unit on the farm. Most are also considering adding new dryers, but timing is important, with manufacturers producing only so many units per year. It’s one more example, Spieser says, that shows the value of planning. CG